Гальваническая обработка: нетривиальные решения и практический опыт
В этой статье мы не будем подробно останавливаться на базовых принципах гальванотехники, которые хорошо известны каждому специалисту. Вместо этого мы рассмотрим ряд нестандартных ситуаций и сложных случаев, возникающих при гальванической обработке металлов, а также поделимся практическим опытом их решения.
Хромирование: борьба с водородным охрупчиванием
Проблема водородного охрупчивания при хромировании
Электролитическое хромирование — один из самых востребованных процессов гальванотехники, позволяющий значительно повысить твердость, износостойкость и коррозионную стойкость изделий. Однако этот процесс имеет и обратную сторону - риск водородного охрупчивания обрабатываемых деталей.
Во время хромирования ионы водорода, присутствующие в электролите, восстанавливаются на катоде (детали) и проникают в кристаллическую решетку металла. Это приводит к возникновению внутренних напряжений и повышению хрупкости, что особенно критично для деталей, работающих в условиях циклических нагрузок или агрессивных сред.
Стандартные рекомендации по снижению наводороживания - уменьшение катодной плотности тока и повышение температуры электролита - не всегда позволяют полностью решить проблему, особенно при хромировании деталей сложной конфигурации или изготовленных из высокопрочных сталей.
Альтернативные электролиты для снижения охрупчивания
Одним из наиболее перспективных направлений борьбы с водородным охрупчиванием является использование специальных электролитов с добавками, снижающими наводороживание.
Электролит | Состав | Рабочая температура, °C | Плотность тока, А/дм² | Степень наводороживания | Особенности |
---|---|---|---|---|---|
Стандартный хромовый электролит | Хромовый ангидрид, серная кислота | 50-60 | 20-50 | Высокая | Низкая стоимость, широкая доступность, но высокая степень наводороживания |
Электролит с добавкой фтористого натрия | Хромовый ангидрид, серная кислота, фтористый натрий | 40-50 | 30-60 | Сниженная | Снижает наводороживание, но требует более точного контроля параметров |
Электролит с добавкой сульфата кобальта | Хромовый ангидрид, серная кислота, сульфат кобальта | 30-40 | 40-80 | Низкая | Позволяет получать покрытия с низким внутренним напряжением, но более дорогой |
Электролит с добавкой органических соединений | Хромовый ангидрид, серная кислота, специальные органические добавки | 20-30 | 50-100 | Очень низкая | Обеспечивает минимальное наводороживание, но требует использования специального оборудования и тщательной подготовки поверхности |
- Таблица 1. Сравнительные характеристики различных электролитов для хромирования
Выбор оптимального электролита зависит от многих факторов: марки стали, требований к твердости и износостойкости покрытия, конфигурации детали и др.
Например, при хромировании пружинных элементов из высокопрочной стали, работающих на изгиб, критически важным является минимизация водородного охрупчивания. В данном случае оправдано применение электролитов с органическими добавками, даже несмотря на их высокую стоимость.
Термообработка после хромирования
Даже при использовании электролитов с низким наводороживанием часть водорода все равно проникает в структуру металла. Для его удаления и снятия внутренних напряжений применяют термообработку после хромирования - низкотемпературный отпуск.
Важно правильно подобрать температуру и время выдержки при отпуске. Слишком низкая температура будет неэффективна для удаления водорода, а слишком высокая может привести к снижению твердости хромового покрытия.
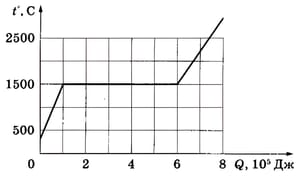
Рис. 1. Зависимость остаточного напряжения в стали от температуры отпуска после хромирования
Например, при разработке технологического процесса хромирования вала ответственного назначения была экспериментально подобрана оптимальная температура отпуска - 180°C, время выдержки - 4 часа. Это позволило снизить уровень остаточных напряжений до допустимого значения, сохранив при этом требуемую твердость хромового покрытия.
Контроль наводороживания
Для обеспечения стабильно высокого качества хромированных деталей и предотвращения брака по водородному охрупчиванию необходим тщательный контроль на всех этапах процесса.
Существуют различные методы определения количества водорода в металле после хромирования, например:
- Метод вакуумной экстракции - позволяет точно определить общее количество водорода в образце, но требует специального оборудования и является достаточно трудоемким.
- Метод Барнса - основан на измерении давления водорода, выделяющегося из образца при нагреве. Менее точен, чем вакуумная экстракция, но более оперативен.
- Электрохимические методы - позволяют оценить концентрацию водорода на поверхности металла, что может служить косвенным показателем его общего содержания.
На одном из производств, где я работал, была внедрена система экспресс-контроля наводороживания с использованием электрохимического метода. Это позволило оперативно отслеживать качество процесса хромирования и своевременно вносить коррективы в случае отклонений от нормы.
Цинкование: достижение равномерного покрытия на сложной форме
Проблема - неравномерность покрытия на деталях сложной конфигурации
Цинкование – один из самых распространенных и эффективных методов защиты стальных изделий от коррозии. Однако при цинковании деталей сложной формы - с глубокими углублениями, отверстиями, резкими переходами - возникает серьезная проблема - неравномерность толщины покрытия.
На выступающих участках и острых краях плотность тока обычно выше, чем на вогнутых поверхностях и в углублениях. Это приводит к тому, что на выступах цинк осаждается быстрее и покрытие получается более толстым, в то время как в углублениях оно может быть слишком тонким или вообще отсутствовать.
На распределение тока в гальванической ванне влияют многие факторы:
- Геометрия детали: чем более сложная форма, тем более неравномерным будет распределение тока.
- Расположение анодов: чем ближе анод расположен к определенному участку детали, тем выше плотность тока на этом участке.
- Состав электролита: некоторые электролиты обладают лучшей рассеивающей способностью, чем другие, то есть способны формировать более равномерное покрытие.
Компьютерное моделирование для оптимизации процесса
В настоящее время для решения проблемы неравномерности покрытия при цинковании деталей сложной формы широко используются методы компьютерного моделирования. С помощью специализированного программного обеспечения можно смоделировать распределение электромагнитного поля в гальванической ванне с учетом геометрии детали, расположения анодов, состава электролита и других параметров.
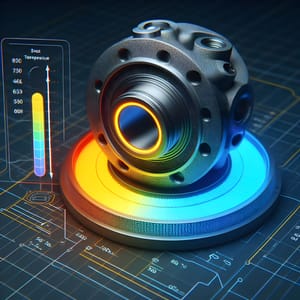
Рис. 2. Результат моделирования распределения тока при цинковании детали сложной формы
Это позволяет еще на этапе проектирования технологического процесса:
- Определить зоны детали, на которых возможны отклонения толщины покрытия.
- Подобрать оптимальную конфигурацию анодов: их форму, размеры, расположение относительно детали.
- Оценить эффективность использования дополнительных электродов, экранов, формирователей электромагнитного поля.
- Выбрать электролит с наилучшей рассеивающей способностью.
Например, при разработке технологии цинкования корпуса сложной формы для одного из наших за заказчиков было проведено компьютерное моделирование, которое показало значительную неравномерность толщины покрытия при использовании стандартного расположения анодов. После корректировки конфигурации анодов с учетом рекомендаций программы удалось добиться равномерного распределения тока и получить покрытие с требуемыми характеристиками.
Использование специальных анодов
Помимо компьютерного моделирования, для получения равномерного цинкового покрытия на деталях сложной формы применяют и другие подходы:
- Аноды сложной формы: в некоторых случаях для более равномерного распределения тока используют аноды, повторяющие форму детали или ее отдельных участков.
- Конформные аноды: это гибкие аноды, которые можно придать любую форму в зависимости от конфигурации детали.
- Аноды с регулируемой плотностью тока: позволяют изменять плотность тока на разных участках анода, что дает возможность компенсировать неравномерность распределения тока, обусловленную геометрией детали.
На одном из предприятий, с которыми мне пришлось работать, стояла задача нанесения равномерного цинкового покрытия на внутреннюю поверхность полой трубы диаметром 100 мм и длиной 1 метр. Было принято решение использовать специальный анод в виде стержня, помещенного внутри трубы. Для обеспечения равномерного распределения тока по длине трубы анод был разделен на несколько секций, каждая из которых подключалась к источнику питания через отдельный резистор. Регулируя сопротивление резисторов, удалось добиться одинаковой плотности тока на всех участках анода и получить равномерное покрытие на внутренней поверхности трубы.
Выбор оптимального электролита
Состав электролита также оказывает существенное влияние на равномерность цинкового покрытия, особенно на деталях сложной формы.
- Электролиты с высокой рассеивающей способностью способны формировать более равномерное покрытие, даже при неидеальном распределении тока.
- Электролиты с низкой рассеивающей способностью, напротив, склонны к образованию "наплывов" на выступающих участках и "непрокрытий" в углублениях.
Рекомендации по выбору электролита:
- Для цинкования деталей простой формы можно использовать цианистые электролиты - они обладают высокой рассеивающей способностью, но токсичны.
- Для деталей сложной конфигурации лучше выбирать менее токсичные щелочные электролиты с добавками, повышающими рассеивающую способность.
- При высоких требованиях к равномерности покрытия следует обратить внимание на слабокислые электролиты, которые обеспечивают наиболее равномерное распределение металла.
Важно помнить, что выбор электролита - это всегда компромисс между рассеивающей способностью, скоростью осаждения, качеством покрытия и экологической безопасностью.
Многослойные покрытия: когда одно покрытие хорошо, а два - лучше
Преимущества многослойных покрытий
В ряде случаев нанесение нескольких гальванических покрытий позволяет добиться уникальных эксплуатационных характеристик, которые невозможно получить при использовании только одного металла.
Комбинируя разные покрытия, можно:
- Значительно повысить коррозионную стойкость изделий, особенно в условиях воздействия агрессивных сред.
- Увеличить твердость и износостойкость поверхности.
- Улучшить декоративные свойства, например, придать изделию привлекательный блеск или особый цвет.
Совместимость металлов
При создании многослойных покрытий важно учитывать электрохимическую совместимость металлов. Не все металлы можно осаждать друг на друга без риска ухудшения свойств покрытия.
- Если металл покрытия имеет более электроотрицательный потенциал, чем металл основы, то он будет служить анодом в образующейся гальванической паре. В этом случае покрытие будет защищать основу от коррозии, разрушаясь само (протекторная защита).
- Если же потенциал покрытия более электроположительный, то анодом будет служить основа. Это может привести к ускоренной коррозии основы в местах повреждения покрытия (контактная коррозия).
В таблице 2 приведена информация о совместимости некоторых металлов, часто используемых в гальванотехнике.
Металл основы | Совместимые покрытия | Несовместимые покрытия |
---|---|---|
Сталь | Zn, Cd, Al, Ni, Cu, Sn, Ag, Au | |
Медь | Ni, Cr, Ag, Au | Zn, Cd, Al, Sn |
Алюминий | Zn, Sn, Cr | Cu, Ni, Ag, Au |
- Таблица 2. Совместимость металлов для гальванических покрытий
Примеры удачных комбинаций
Рассмотрим несколько примеров удачных сочетаний гальванических покрытий, которые часто используются в промышленности:
- Медь - никель - хром: классическая система покрытий, обеспечивающая высокую коррозионную стойкость, износостойкость и привлекательный внешний вид. Медь служит подслоем для никеля, улучшая адгезию и выравнивая поверхность. Никель обеспечивает основную защиту от коррозии, а хром придает покрытию твердость, износостойкость и декоративный блеск.
- Цинк - никель: используется для защиты стальных деталей от коррозии в условиях высокой влажности и воздействия солей. Никель в данном случае служит барьерным слоем, предотвращающим контакт цинка с агрессивной средой и замедляющим процесс его разрушения.
- Никель - золото: применяется в электронике, ювелирном деле и других областях, где требуется сочетание высокой коррозионной стойкости, электропроводности и привлекательного внешнего вида.
На одном из предприятий, где я работал, стояла задача повысить износостойкость и жаростойкость режущего инструмента, работающего в условиях высоких температур и абразивного износа. Было разработано и внедрено многослойное покрытие, состоящее из трех слоев:
- Никелевый подслой: обеспечивал надежную адгезию к основному металлу инструмента.
- Хромо-нитридное покрытие: создавало твердую и износостойкую поверхность.
- Тонкий слой твердого смазочного материала: снижал трение и предотвращал налипание стружки.
Такое комбинированное покрытие позволило значительно увеличить ресурс инструмента и повысить качество обработки.
Особенности контроля качества многослойных покрытий
Контроль качества многослойных покрытий представляет собой более сложную задачу по сравнению с однослойными. Необходимо оценивать не только характеристики каждого слоя (толщину, адгезию, пористость и т. д.), но и их взаимодействие друг с другом.
Методы контроля:
- Микроскопия: позволяет оценить толщину каждого слоя, выявить дефекты структуры, определить наличие пор и трещин.
- Рентгенофлуоресцентный анализ: позволяет определить элементный состав каждого слоя и выявить возможные примеси.
- Адгезионные испытания: проводятся для оценки прочности сцепления отдельных слоев друг с другом и с основным металлом.
- Коррозионные испытания: проводятся для оценки защитных свойств многослойного покрытия в целом.
На одном из предприятий автомобильной промышленности, где я консультировал, возникла проблема с качеством декоративных хромированных элементов кузова. После нескольких месяцев эксплуатации на поверхности хрома появлялись пятна и вздутия. Анализ показал, что причина брака - в нарушении технологии нанесения многослойного покрытия медь-никель-хром.
Для решения проблемы были внедрены дополнительные этапы контроля:
- Контроль толщины и пористости никелевого подслоя после каждой операции.
- Внедрение испытаний на адгезию между слоями никеля и хрома.
Это позволило выявить и устранить причины брака на ранних стадиях и значительно повысить качество хромированных деталей.
Заключение
В этой статье мы рассмотрели лишь некоторые из множества задач, возникающих при гальванической обработке металлов. Этот технологический процесс, казалось бы, давно изученный и отработанный, на самом деле таит в себе еще множество секретов и подводных камней.
Постоянное усложнение конструкций изделий, повышение требований к их эксплуатационным характеристикам, внедрение новых материалов - все это заставляет специалистов по гальванотехнике постоянно совершенствовать технологические процессы, искать новые решения и не бояться экспериментировать.