Лазерная резка металла: 15 лет на передовой
Когда в середине 2000-х я начинал свой путь в металлообработке, лазерная резка казалась чем-то из области фантастики. Дорого, сложно, доступно лишь избранным. Первые годы работы прошли в мире фрез, токарных станков, плазменной резки. Но интерес к лазеру не угасал. Изучал статьи, общался с теми, кто уже работал с этой технологией. Когда появилась возможность приобрести свой первый лазерный станок, сомнений не было.
С тех пор лазерная резка стала неотъемлемой частью моей работы, настоящей страстью. Меня всегда привлекали нестандартные задачи, поиск новых возможностей. Работа с лазером – это постоянный вызов, поиск баланса между точностью и скоростью, борьба за каждый миллиметр чистого реза.
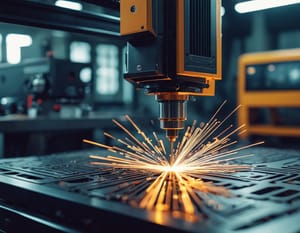
За годы работы были и успехи, и разочарования, и сломанные станки, и ночи, проведенные за поиском решения нетривиальной задачи. Но главное - пришло понимание: лазер - это не просто инструмент, это ключ к совершенно новым возможностям в мире металла.
Неочевидные нюансы выбора параметров резки
За годы работы с лазерной резкой я резал, наверное, все марки стали, которые только можно найти на рынке. И знаете, что я понял? Таблицы параметров, которые дают производители станков - это лишь отправная точка. Реальность гораздо сложнее и интереснее. Вроде бы всё просто: выбираешь материал, указываешь его толщину, станок сам подбирает мощность и скорость. Но на практике часто приходится отклоняться от этих рекомендаций, искать свои, нестандартные решения.
И дело не только в капризах оборудования. Сталь - материал живой. Одна и та же марка стали, но от разных производителей, может вести себя по-разному при лазерной резке. Влияет и состояние материала: наличие внутренних напряжений, микротрещин, неравномерность структуры. Все эти факторы приходится учитывать, чтобы добиться идеального результата.
Марка стали: не все так просто
Возьмём, к примеру, углеродистую сталь. Казалось бы, чем выше содержание углерода, тем тверже материал, тем больше мощности лазера нужно для резки. В теории - да. Но на практике сталкивался с ситуациями, когда сталь с низким содержанием углерода резалась хуже, чем высокоуглеродистая. Причина крылась в структуре материала: из-за особенностей прокатки в стали образовывались микротрещины, которые приводили к неравномерному проплавлению.
В таких случаях приходилось действовать методом проб и ошибок. Снижал мощность лазера, менял скорость резки, экспериментировал с газом. Иногда помогало изменение фокусного расстояния: смещение фокуса вверх или вниз может существенно повлиять на качество реза. Поиск оптимальных параметров для каждой партии стали - это отдельная задача, которая требует внимательности и опыта.
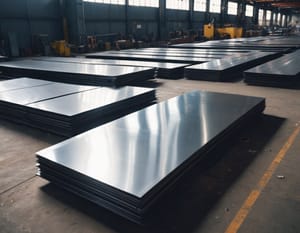
Газ: экономия - не всегда хорошо
Выбор газа - отдельная история. Кислород - дешевле, дает большую скорость резки, но оставляет оксидную пленку. Азот - дороже, скорость резки ниже, но рез получается чистым, без окалины. Казалось бы, выбор очевиден: для черных металлов - кислород, для нержавейки - азот. Но на практике все оказывается сложнее.
Однажды столкнулся с задачей резки тонкой нержавеющей стали. Использовал азот, все по технологии. Но рез получался неровным, с заусенцами. Долго искал причину, пока не обратил внимание на чистоту азота. Оказалось, в газе были примеси кислорода, буквально сотые доли процента. Казалось бы, ерунда, но именно они портили весь процесс. Перешел на азот более высокой чистоты - проблема исчезла.
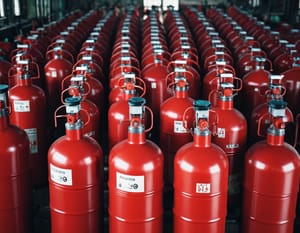
Эта история научила меня важному уроку: иногда дело не в самих параметрах резки, а в качестве расходных материалов. Чистота газа, качество защитного стекла, даже состав охлаждающей жидкости - все это может влиять на результат.
Фокусное расстояние: игра миллиметров
Фокусное расстояние - это тоже не просто цифра в настройках станка. Меняя фокус, мы меняем форму лазерного луча, а значит, и характеристики реза. Для тонких материалов нужен узкий фокус, для толстых - более широкий. Это базовые знания, которые есть у каждого оператора лазерной резки.
Но и тут есть место для экспериментов. Однажды нужно было вырезать сложный контур в листе толстой стали. Стандартный подход с широким фокусом не давал нужной точности. Углы получались закругленными, рез - недостаточно четким. Решил попробовать узкий фокус, снизил скорость резки - и получил идеальный рез. Все линии - четкие, углы - острые, никаких закруглений. Да, время резки увеличилось, но результат того стоял.
С тех пор я всегда помню: не стоит бояться отходить от стандартных решений. Иногда небольшое изменение фокусного расстояния может дать поразительный результат.
Импульсный режим: не только для гравировки
Импульсный режим часто используется для гравировки, но и в резке он может пригодиться. Меняя частоту импульсов, мы можем регулировать тепловой режим резки. Это позволяет резать материалы, склонные к перегреву, например, тонкий алюминий или медь. В непрерывном режиме эти материалы часто плавятся, деформируются, рез получается некачественным.
Однажды нужно было вырезать мелкие детали из меди. В непрерывном режиме медь плавилась и деформировалась, детали получались бракованными. Перешел на импульсный режим, начал экспериментировать с частотой импульсов. Нашел оптимальную частоту - и получил идеальные детали без деформаций. Рез - чистый, ровный, без признаков перегрева.

Этот пример показывает, что импульсный режим - это не только инструмент для гравировки. Он может быть полезен и в резке, особенно при работе с тонкими и чувствительными к перегреву материалами.
"Болезни" станков и их лечение
Любой, кто хоть сколько-нибудь серьезно работал с лазерными станками, знает: эти машины, как и люди, подвержены различным "болезням". За годы работы мне пришлось столкнуться с целым букетом проблем, от банального загрязнения оптики до серьезных поломок электроники. И скажу честно, не всегда помогали стандартные решения от производителей. Приходилось импровизировать, искать обходные пути, разбираться в принципах работы станка на уровне железа.
В какой-то момент я понял, что знаю свой станок лучше, чем инженеры сервисного центра. Это не хвастовство, это необходимость. Когда производство стоит, а сервис не может приехать неделю, приходится становиться и механиком, и электронщиком, и программистом.
Но даже самый надежный станок когда-нибудь ломается. И важно не просто уметь его починить, но и понимать, почему произошла поломка, как ее предотвратить в будущем. Это приходит с опытом, с внимательным отношением к оборудованию, с пониманием процессов, которые происходят внутри лазерного станка.
Диагностика - всему голова
Первый шаг к решению любой проблемы - правильная диагностика. Иногда причина неисправности очевидна: например, рез становится неровным из-за загрязнения защитного стекла. Но бывают ситуации намного сложнее. Однажды станок стал выдавать странные ошибки позиционирования. Лазерная головка двигалась рывками, не попадала в нужные точки, рез получался кривым.
Проверили все очевидные вещи: калибровку, состояние направляющих, натяжение ремней. Ничего не помогало. Начали изучать логи станка, анализировать работу электроники. В итоге оказалось, что виноват неисправный датчик температуры окружающей среды. Станок получал неправильные данные о температуре и корректировал работу приводов с учетом этих данных. Замена датчика решила проблему.
Эта история показала мне, насколько важна внимательная диагностика. Иногда причина неисправности лежит совсем не там, где ее ищешь.
Народная мудрость и обходные пути
Иногда стандартные методы ремонта не работают. В таких случаях приходится полагаться на собственный опыт, интуицию и даже "народные" хитрости. Однажды сломался блок управления газовым клапаном. Заказать новый - долго и дорого. Производство стоит, сроки горят, надо что-то делать.
Нашел на форуме совет от такого же "кулибина", как я: использовать обычный электромагнитный клапан от стиральной машины. Стоимость - копейки, найти можно на любой разборке. Купил клапан, немного доработал - и станок заработал. Конечно, это временное решение, но оно позволило продолжить работу и выполнить срочный заказ.
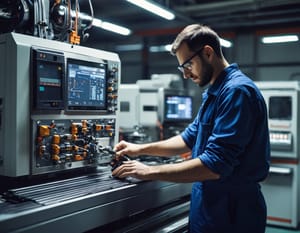
Эта история научила меня не бояться нестандартных решений. Иногда самый простой и дешевый способ - самый эффективный.
Опыт - лучший учитель
За время работы я перепробовал разные станки: от простых китайских моделей до сложных европейских систем. И понял, что у каждой марки свои "болячки", свои слабые места. Китайские станки часто грешат некачественной электроникой, европейские - слишком "умные" и капризные в настройке.
Но со временем приходит понимание, где нужно быть внимательнее, что проверять в первую очередь, какие запчасти лучше держать про запас. У каждого станка свой характер, свои привычки. И только хорошо зная эти привычки, можно обеспечить стабильную и эффективную работу.
Оптимизация процесса лазерной резки
Лазерная резка сама по себе - высокотехнологичный процесс. Но даже с самым современным оборудованием всегда есть место для оптимизации. За годы работы я выработал несколько принципов, которые позволяют "выжать" максимум из лазерного станка: минимизировать отходы, увеличить скорость работы, повысить эффективность охлаждения. Это не просто вопросы экономии, хотя и это важно. Это вопросы эффективности всего производства, возможности брать более сложные и интересные заказы.
Иногда достаточно небольших изменений в технологическом процессе, чтобы добиться значительного прироста производительности. Главное - не бояться экспериментировать, искать нестандартные решения, анализировать результаты.
Раскрой: не только геометрия
Правильный раскрой - это не только уложить детали на листе металла максимально плотно. Это базовый уровень, которому учат на первых курсах инженеров. Но есть и более тонкие моменты, которые приходят с опытом. Важно учитывать особенности лазерной резки, понимать, как тепло распространяется в листе металла во время резки.
Например, начинать рез лучше с внутренних контуров, а затем переходить к внешним. Это снижает риск деформации деталей из-за нагрева. Если сначала вырезать внешний контур, то внутренняя часть детали может перегреться и деформироваться. Еще один нюанс - ориентация деталей относительно направления проката металла. Резать вдоль проката легче и быстрее, чем поперек. Это связано с анизотропией свойств металла, которая возникает при прокатке. Иногда стоит немного повернуть деталь на листе, чтобы добиться лучшего результата.
Программное обеспечение: не все CAM-системы одинаково полезны
Существует множество программ для создания раскроя и генерации G-кода для лазерных станков. Но не все они одинаково эффективны. Некоторые CAM-системы фокусируются только на плотности упаковки деталей, не учитывая особенности лазерной резки. Они могут генерировать не оптимальные траектории движения лазерной головки, что приводит к увеличению времени резки и перерасходу энергии.
Другие CAM-системы слишком сложны в использовании и требуют много времени на освоение. Их функционал избыточен для большинства задач, а сложность интерфейса отпугивает новичков. Лично я предпочитаю программы, которые позволяют гибко настраивать параметры резки для каждой детали, учитывать разные виды материалов, генерировать оптимальные траектории движения лазерной головки. При этом они должны быть простыми в использовании, интуитивно понятными.
Автоматизация: роботы спешат на помощь
В условиях серийного производства ручная подача материала и выгрузка деталей - это узкое место. Это медленно, неэффективно, требует больших затрат ручного труда. Роботизация процесса позволяет значительно увеличить производительность. Робот может работать круглосуточно, не устает, не делает ошибок. Он не нуждается в перерывах, отпусках, больничных.
Я внедрял роботов на нескольких производствах и видел, как это меняет общую картину. Производительность вырастает в разы, себестоимость продукции снижается, качество повышается. Конечно, внедрение роботов требует инвестиций, но в долгосрочной перспективе это окупается. И чем раньше вы начнете внедрять роботизацию, тем быстрее получите отдачу от инвестиций.
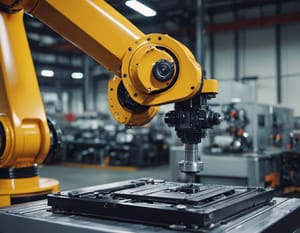
Охлаждение: не допускайте перегрева
Эффективное охлаждение - залог долгой жизни лазерного станка. Производители оборудования предлагают стандартные системы охлаждения, но иногда их недостаточно. Например, в жарком климате или при интенсивной эксплуатации станка стандартная система может не справляться. Это приводит к перегреву лазера, электроники, механических узлов. А перегрев - это ускоренный износ, снижение точности, повышенный риск поломок.
В таких случаях приходится искать нестандартные решения. Я экспериментировал с разными типами охлаждающей жидкости, устанавливал дополнительные радиаторы, модернизировал системы вентиляции. Главное - не допускать перегрева лазера и электроники, поддерживать оптимальный тепловой режим работы станка. Это позволит продлить срок службы оборудования и обеспечить стабильную работу.
Сложности лазерной резки "неметалла"
Когда говоришь "лазерная резка", большинство людей представляет себе металлические детали, станки с мощными лазерами. Но лазер - это универсальный инструмент. Он может резать не только металл, но и разнообразные неметаллические материалы: дерево, пластик, композиты. Я давно интересовался этими возможностями лазера, экспериментировал, искал новые применения для своей "лазерной мастерской".
Работать с "неметаллом" оказалось не так просто, как я думал сначала. Каждый материал обладает своими особенностями, требует своего подхода, своих параметров резки. Приходилось много экспериментировать, искать информацию, советоваться с коллегами. Но результат того стоил: лазер открыл передо мной новые горизонты, новые возможности для творчества.
Дерево: не все так просто
Казалось бы, резать дерево лазером - проще простого. Материал мягкий, легко поддается обработке. Но и тут есть свои нюансы. Во-первых, дерево - материал не однородный. Разные породы дерева имеют разную плотность, твердость, содержание смолы. Это влияет на выбор параметров резки. Слишком большая мощность лазера может привести к обугливанию древесины, слишком малая - к неровному резу.
Во-вторых, дерево горит. При лазерной резке важно правильно подобрать мощность лазера и скорость резки, чтобы не допустить возгорания. Я пробовал разные подходы: использование воздуха в качестве вспомогательного газа, уменьшение мощности лазера, увеличение скорости резки. В итоге выработал свои "рецепты" для разных пород дерева. Например, для резки фанеры я использую небольшую мощность лазера и высокую скорость резки, а для резки дуба - большую мощность и низкую скорость.
Оргстекло: борьба с плавлением
Оргстекло - популярный материал для лазерной резки. Из него делают вывески, сувениры, детали интерьера. Но и тут есть свои сложности. Оргстекло легко плавится под действием лазера. Края реза могут быть неровными, с заусенцами. Это портит внешний вид изделия, снижает его качество.
Для борьбы с плавлением я использовал разные методы: охлаждение зоны резки сжатым воздухом, применение специальной защитной пленки, уменьшение мощности лазера. Важно найти баланс между скоростью резки и качеством реза. Слишком быстрая резка приводит к плавлению, слишком медленная - к обугливанию материала.
Композиты: сложно, но возможно
Композитные материалы - это сочетание разных материалов с разными свойствами. Например, углепластик - это композит из углеродных волокон и эпоксидной смолы. Резка композитов лазером - сложная задача. Разные компоненты материала по-разному реагируют на лазерное излучение. Это может привести к неравномерному проплавлению, образованию окалины, выделению вредных газов.
Я проводил тесты с разными типами композитов, менял параметры резки, экспериментировал с газами. Задача осложняется тем, что состав композитных материалов может сильно варьироваться в зависимости от производителя. В итоге удалось найти подходы для резки некоторых видов композитов. Но это всегда вызов, всегда поиск компромисса между скоростью, качеством и безопасностью.
Будущее за гибридами?
В начале моей карьеры лазерный станок казался самодостаточной единицей. Режешь листовой металл - вот и всё производство. Но технологии не стоят на месте. Сегодня лазерная резка все чаще становится частью более сложных процессов, интегрируется с другими методами обработки: гибкой, сваркой, фрезеровкой. Это позволяет создавать более сложные и интересные изделия, повышать производительность, снижать себестоимость.
Я вижу в этой тенденции не просто технический прогресс, а смену самой парадигмы металлообработки. Мы переходим от отдельных операций к комплексному подходу, от универсальных станков к специализированным, от ручного труда к автоматизации.
Гибка + лазер: идеальная пара
Сочетание лазерной резки и гибки - очевидный симбиоз. Вырезаешь заготовку лазером, сгибаешь ее на гибочном прессе - и получаешь готовую деталь. Я использовал такой подход во многих проектах. Например, изготавливал корпуса для электронного оборудования, детали вентиляционных систем, элементы металлической мебели.
Лазерная резка позволяет вырезать сложные контуры с высокой точностью, гибка - придать заготовкам нужную форму. При этом важно учитывать влияние гибки на геометрию детали, правильно рассчитывать размеры заготовки. Существуют специальные программы, которые помогают с этим.
Лазер + сварка: расширяем возможности
Лазерная сварка - еще одна технология, которая хорошо дополняет лазерную резку. Лазерная сварка позволяет соединять детали с высокой точностью, минимальной зоной термического влияния. Это особенно важно при работе с тонкими и чувствительными к перегреву материалами.
Я использовал лазерную сварку для создания различных металлоконструкций, от небольших кронштейнов до крупных рам. Лазерная резка позволяла вырезать детали с нужными размерами и формой, лазерная сварка - соединить их в единое целое. При этом важно правильно подобрать параметры сварки, чтобы обеспечить прочность и надежность соединения.
Лазер + фрезеровка: точность и универсальность
Фрезерная обработка - более универсальный метод, чем лазерная резка. Фреза может не только резать, но и сверлить, делать пазы, нарезать резьбу. Я использовал фрезеровку для обработки деталей, вырезанных лазером. Например, делал фаски, сверлил отверстия, нарезал резьбу.
Сочетание лазерной резки и фрезеровки позволяет создавать детали сложной геометрии с высокой точностью. Это особенно важно при изготовлении деталей для машиностроения, приборостроения, авиационной и космической промышленности.
Взгляд в будущее: гибридные системы
Я вижу большое будущее за гибридными системами, которые будут сочетать в себе несколько методов обработки. Например, представьте себе станок, который может резать лазером, гнуть, сваривать и фрезеровать. Такой станок будет по-настоящему универсальным инструментом для металлообработки. Уверен, что в ближайшем будущем мы увидим появление таких систем.
Годы работы с лазерной резкой научили меня главному: технологии постоянно развиваются. То, что еще вчера казалось фантастикой, сегодня становится реальностью. И кто знает, какие еще возможности откроет перед нами лазерная резка в будущем. Главное - не бояться нового, экспериментировать, искать нестандартные решения.