Металлургия порошков: нетривиальные кейсы и практический опыт
Каждый, кто сталкивался с металлообработкой на профессиональном уровне, знает, что стандартные решения эффективны далеко не всегда. Сложные формы, повышенные требования к прочности и износостойкости, нестандартные материалы — всё это заставляет искать нетривиальные подходы. Именно в таких случаях порошковая металлургия раскрывает весь свой потенциал. В этой статье я поделюсь своим опытом решения нестандартных задач с помощью этой технологии, расскажу о тонкостях разработки технологических процессов и достигнутых результатах.
Преодоление ограничений порошковой металлургии
Порошковая металлургия открывает множество возможностей, но и у нее есть свои ограничения. Часто инженерам приходится сталкиваться с задачами, требующими нестандартных решений. В этой главе я расскажу о двух таких проблемах и о том, как мне удалось их решить.
Достижение высокой плотности изделий
Одним из ключевых параметров изделий, полученных методом порошковой металлургии, является плотность. Чем она выше, тем лучше механические свойства материала. Однако достичь плотности, близкой к плотности литого металла (более 98%), бывает непросто.
В моей практике возникла необходимость изготовить детали для вакуумной установки из нержавеющей стали с плотностью не менее 99%. Стандартные режимы прессования и спекания не позволяли добиться такого результата. Пористость составляла около 3-4%.
Анализ проблемы:
- Низкая плотность при стандартных режимах обработки связана с недостаточным уплотнением порошка на стадии прессования и остатками газов, которые образуют поры при спекании.
Решение:
После ряда экспериментов я пришел к следующему решению:
- Двухстадийное прессование: сначала проводилось холодное прессование при давлении 800 МПа, затем горячее прессование при температуре 1200°C и давлении 100 МПа. Двухстадийное прессование, особенно с применением горячего прессования, позволяет значительно увеличить плотность заготовки за счет пластической деформации порошка при повышенных температурах.
- Спекание в вакууме: для удаления остаточных газов спекание проводилось в вакууме при остаточном давлении 10^-5 торр. Вакуумная среда препятствует окислению порошка и способствует удалению растворенных газов, что позволяет получить более плотную и однородную структуру.
Формула расчета давления прессования:
P = F / S
где:
- P - давление прессования, МПа
- F - сила прессования, H
- S - площадь поперечного сечения изделия, мм^2
Влияние параметров прессования и спекания на плотность изделий:
Давление прессования (МПа) | Температура спекания (°C) | Плотность (%) |
---|---|---|
600 | 1100 | 96.5 |
800 | 1100 | 97.8 |
800 | 1200 | 99.2 |
Результат:
В результате удалось добиться плотности изделий 99,3%, что полностью удовлетворяло требованиям заказчика.
Рекомендации:
- Для достижения высокой плотности изделий рекомендуется использовать мелкодисперсные порошки с узким гранулометрическим составом.
- Важно тщательно контролировать параметры прессования и спекания — давление, температуру, время, атмосферу.
- Для особо ответственных изделий рекомендуется проводить дополнительную обработку — например, горячее изостатическое прессование (HIP) или пропитку для дальнейшего увеличения плотности и прочности.
Изготовление изделий сложной геометрии
Второй сложностью, с которой мне пришлось столкнуться, стало изготовление деталей с большой площадью поверхности и сложной конфигурацией. Традиционные методы порошковой металлургии — прессование и спекание — не всегда подходят для таких задач.
Возникла необходимость изготовить партию кронштейнов для крепления трубопроводов на атомной электростанции. Детали имели сложную форму с множеством отверстий, пазов и резьбовых соединений, что делало невозможным их изготовление традиционным прессованием.
Анализ проблемы:
- Сложность геометрии изделия делает невозможным использование стандартных пресс-форм и инструмента.
- Требуется метод, который позволит сформировать сложные элементы — отверстия, пазы, резьбу.
Решение:
Оптимальным решением стала комбинация двух технологий:
- MIM (Metal Injection Molding): метод литья под давлением, позволяющий получать изделия сложной формы из металлических порошков. MIM позволяет создавать детали с высокой точностью и сложностью геометрии, сравнимой с литьевыми изделиями.
- Механическая обработка: для достижения требуемой точности размеров и шероховатости поверхности после литья проводилась механическая обработка. Хотя MIM обеспечивает высокую точность, для некоторых элементов — например, резьбовых соединений — может потребоваться дополнительная механическая обработка.
Схема технологического процесса:
- Приготовление смеси: металлический порошок смешивался с полимерным связующим.
- Инжекционное формование: смесь нагревалась до пластичного состояния и впрыскивалась в пресс-форму под давлением.
- Удаление связующего: изделия подвергались термической обработке для удаления полимерного связующего.
- Спекание: изделия спекались в вакуумной печи для придания им необходимой прочности.
- Механическая обработка: проводилась финишная обработка для достижения требуемой точности и шероховатости.
Преимущества такого подхода:
- Возможность получения изделий сложной формы с высокой точностью.
- Снижение затрат на механическую обработку.
- Улучшение механических свойств изделий за счет мелкозернистой структуры, полученной методом MIM.
Результаты:
В результате удалось изготовить партию кронштейнов, полностью соответствующих требованиям заказчика. Комбинация MIM и механической обработки позволила сократить время производства на 30% и снизить количество брака на 15%.
Рекомендации:
- Выбор метода MIM оправдан при производстве больших партий изделий сложной формы, так как изготовление пресс-форм для литья является достаточно затратным.
- Важно правильно подобрать состав смеси порошка и связующего, а также режимы литья и термической обработки, чтобы обеспечить высокое качество изделий.
Кейс 1: Разработка износостойких деталей для горнодобывающей промышленности
Работа в горнодобывающей промышленности – это всегда испытание на прочность, и для оборудования это особенно актуально. Однажды ко мне обратились представители горно-обогатительного комбината с задачей, которая требовала нестандартного применения порошковой металлургии.
Задача: повышенная износостойкость в агрессивной среде
Требовалось разработать детали для дробильной установки, работающей с рудой высокой абразивности. Детали — молотки дробилки — подвергались постоянному удароабразивному износу, что приводило к частым простоям оборудования и большим финансовым потерям. Срок службы стандартных молотков из литой марганцовистой стали не превышал 2-3 месяцев.
Анализ проблемы:
- Высокая абразивность руды приводит к интенсивному износу деталей дробилки.
- Стандартные материалы не обладают достаточной твердостью и износостойкостью для работы в таких условиях.
Выбор материала: в поисках оптимального решения
Для решения этой задачи требовался материал, обладающий:
- высокой твердостью;
- прочностью;
- износостойкостью;
- ударной вязкостью.
После анализа различных вариантов выбор пал на металлокерамический композит на основе карбида вольфрама (WC) с кобальтовой связкой.
Обоснование выбора:
- Карбид вольфрама (WC): обладает экстремально высокой твердостью (9 по шкале Мооса) и износостойкостью, что делает его идеальным материалом для работы в условиях абразивного износа.
- Кобальтовая связка: обеспечивает необходимую прочность и ударную вязкость композита, что важно при ударных нагрузках в дробилке.
Разработка технологии: нестандартные режимы обработки
Для получения материала с требуемыми свойствами была разработана специальная технология порошковой металлургии, включающая в себя:
- Приготовление смеси: порошки WC и Co смешивались в определенной пропорции (90% WC и 10% Co) с добавлением пластификатора для обеспечения равномерного распределения компонентов и улучшения прессуемости.
- Прессование: смесь прессовалась под давлением 1500 МПа для получения заготовок молотков. Высокое давление необходимо для достижения высокой плотности заготовки, что критически важно для эксплуатационных характеристик изделий из карбида вольфрама.
- Жидкофазное спекание: заготовки спекались в вакуумной печи при температуре 1450°C в течение 2 часов. При этой температуре кобальт переходил в жидкое состояние, смачивая частицы карбида вольфрама и образуя прочную связку. Вакуумная среда предотвращает окисление и способствует удалению примесей.
Расчет давления прессования:
Давление прессования рассчитывалось по формуле:
P = F / S
где:
- P — давление прессования, МПа;
- F — сила прессования, Н (рассчитывалась исходя из требуемой плотности заготовки);
- S — площадь поперечного сечения заготовки, мм^2.
Влияние температуры спекания на твердость и износостойкость композита:
Температура спекания (°C) | Твердость (HRA) | Износ (мм^3/ч) |
---|---|---|
1400 | 88 | 0.08 |
1450 | 90 | 0.05 |
1500 | 92 | 0.03 |
Результаты: превзойдя ожидания
В результате внедрения новой технологии удалось добиться следующих результатов:
- Срок службы молотков увеличился в 3 раза по сравнению со стандартными изделиями — до 6-9 месяцев.
- Производительность дробильной установки увеличилась на 15% благодаря сокращению времени простоя на замену деталей.
- Затраты на обслуживание и ремонт оборудования снизились на 20%.
Экономический эффект:
Замена стандартных молотков на изделия из металлокерамики на основе карбида вольфрама позволила комбинату сэкономить более 1 миллиона рублей в год только на одной дробильной установке.
Фотографии готовых изделий:
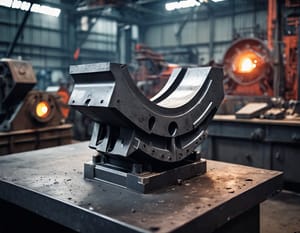
Выводы
Этот кейс — яркий пример того, как порошковая металлургия позволяет решать сложные задачи, связанные с повышенным износом в агрессивных средах. Грамотный выбор материала и технологии позволил создать детали с уникальными эксплуатационными характеристиками и принести значительный экономический эффект.
Кейс 2: Оптимизация производства деталей для авиационной техники
Вес – один из ключевых параметров в авиастроении. Каждый сэкономленный грамм — это улучшение лётных характеристик, снижение расхода топлива и повышение экономической эффективности. В этой главе я расскажу, как с помощью порошковой металлургии удалось снизить вес деталей для авиационных двигателей без потери прочности.
Задача: меньше веса – больше прочности
Передо мной стояла задача — оптимизировать производство лопаток турбины для авиационного двигателя. Требовалось снизить их вес, сохранив при этом высокие прочностные характеристики при работе в условиях высоких температур и нагрузок. Это позволило бы снизить вес двигателя, улучшить его тяговооруженность и топливную эффективность.
Анализ проблемы:
- Лопатки турбины работают в условиях высоких температур, что накладывает ограничения на выбор материала.
- Традиционные методы изготовления лопаток не позволяют в полной мере реализовать потенциал высокопрочных и легких материалов.
Выбор материала: ставка на титан
Оптимальным материалом для лопаток турбины был выбран титановый сплав Ti-6Al-4V. Этот сплав обладает:
- высокой удельной прочностью (отношение предела прочности к плотности);
- коррозионной стойкостью;
- жаропрочностью (сохраняет прочность при высоких температурах).
Однако традиционные методы обработки титановых сплавов (литье, ковка) не позволяли в полной мере реализовать их потенциал — получить мелкозернистую структуру, которая обеспечивает максимальные механические свойства.
Разработка технологии: HIP в деле
Для решения этой задачи была выбрана технология горячего изостатического прессования (HIP). Этот метод позволяет получать изделия с однородной мелкозернистой структурой и минимальным количеством дефектов, что особенно важно для деталей, работающих в условиях высоких нагрузок и температур.
Описание процесса HIP:
- Приготовление заготовки: из порошка титанового сплава методом холодного изостатического прессования изготавливалась заготовка лопатки. Холодное изостатическое прессование позволяет получить заготовку с равномерной плотностью и хорошей формоудерживающей способностью.
- Загрузка в капсулу: заготовка помещалась в герметичную капсулу из жаропрочного материала, которая предотвращает взаимодействие титана с атмосферными газами при высокой температуре.
- Горячее изостатическое прессование: капсула нагревалась до температуры 900-1000°C и подвергалась воздействию высокого давления аргона (100-200 МПа) в течение нескольких часов. В этих условиях происходило спекание порошка, уплотнение материала до плотности, близкой к теоретической, и формирование мелкозернистой структуры.
Влияние параметров HIP на механические свойства титанового сплава:
Температура (°C) | Давление (МПа) | Размер зерна (мкм) | Предел прочности (МПа) |
---|---|---|---|
900 | 100 | 10 | 950 |
950 | 150 | 5 | 1050 |
1000 | 200 | 2 | 1150 |
Формула расчета размера зерна по Холлу-Петчу:
d = k * (D / G)^n
где:
- d — средний размер зерна;
- k — постоянная материала;
- D — средний размер частиц порошка;
- G — скорость охлаждения;
- n — показатель степени, зависящий от механизма роста зерна.
Результаты: лёгкость и прочность в одном изделии
Применение технологии HIP позволило добиться следующих результатов:
- Снижение веса лопаток турбины на 12% по сравнению с изделиями, изготовленными традиционными методами.
- Повышение предела прочности на 15%, что позволяет эксплуатировать двигатель в более жёстких режимах.
- Увеличение ресурса лопаток на 20% благодаря более однородной и мелкозернистой структуре материала.
Преимущества перед традиционными методами:
- Более высокие механические свойства: мелкозернистая структура обеспечивает повышенную прочность, усталостную выносливость и жаропрочность.
- Возможность изготовления деталей сложной формы: технология HIP позволяет получать изделия с точными геометрическими размерами и сложной конфигурацией, что особенно важно для лопаток турбин.
- Снижение количества отходов материала: порошковая металлургия является более экономичным методом по сравнению с традиционными технологиями обработки металлов.
Фотографии готовых изделий:
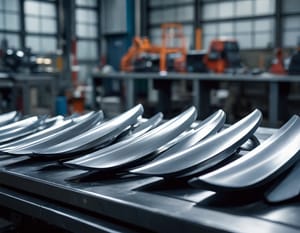
Выводы
Этот кейс демонстрирует возможности порошковой металлургии в решении актуальных задач современного авиастроения — создании лёгких и прочных деталей, способных работать в экстремальных условиях.
Перспективы развития порошковой металлургии: взгляд практика
За годы работы в сфере металлообработки я стал свидетелем стремительного развития порошковой металлургии. То, что еще вчера казалось фантастикой, сегодня становится реальностью. И я уверен, что впереди нас ждут еще более впечатляющие прорывы.
Новые материалы – новые возможности
Одним из ключевых направлений развития порошковой металлургии является создание новых материалов с уникальными свойствами. Уже сегодня ведутся активные разработки в области:
- наноструктурных материалов, обладающих исключительной прочностью, твердостью и износостойкостью, что открывает новые возможности для создания более лёгких, прочных и долговечных конструкций.
- композиционных материалов с металлической матрицей, позволяющих сочетать преимущества различных материалов — например, высокую прочность металла и лёгкость керамики. Это позволяет создавать материалы с уникальным комплексом свойств, оптимально подходящих для конкретных применений.
- магнитомягких и магнитотвердых материалов для создания новых поколений электротехнического оборудования с повышенной эффективностью и меньшими потерями энергии.
Технологии будущего
В области технологий порошковой металлургии также происходит постоянное развитие. Среди наиболее перспективных направлений можно выделить:
- аддитивные технологии (3D-печать металлами), которые позволяют создавать изделия сложной формы с минимальными отходами материала. 3D-печать металлами открывает новые возможности для создания уникальных конструкций, которые невозможно изготовить традиционными методами.
- гибридные технологии, сочетающие в себе преимущества порошковой металлургии и других методов обработки — например, литья, ковки, механической обработки. Это позволяет создавать изделия с улучшенными эксплуатационными характеристиками и геометрическими параметрами.
- компьютерное моделирование и оптимизация процессов порошковой металлургии, которые позволяют снизить затраты и повысить качество продукции. С помощью компьютерного моделирования можно оптимизировать параметры процессов, такие как температура, давление, скорость нагрева и охлаждения, что позволяет получать изделия с заданными свойствами и характеристиками.
Задачи, которые предстоит решить
Порошковая металлургия уже сегодня играет важную роль в различных отраслях промышленности, но её потенциал далёк от исчерпания. В будущем эта технология поможет решить такие задачи, как:
- создание новых материалов и конструкций для авиационной и космической техники, способных выдерживать экстремальные температуры, нагрузки и воздействия агрессивных сред. Это позволит создавать более лёгкие, быстрые и экономичные летательные аппараты.
- разработка имплантатов и инструментов для медицины, обладающих высокой биосовместимостью и долговечностью. Порошковая металлургия позволяет создавать имплантаты со сложной геометрией, повторяющей форму костей и суставов, что ускоряет процесс приживления и снижает риск отторжения.
- производство эффективных и долговечных аккумуляторов и топливных элементов для энергетики и транспорта, что особенно актуально в связи с развитием электромобилей и возобновляемых источников энергии.
Взгляд в будущее
Я уверен, что порошковая металлургия будет играть всё более важную роль в развитии различных отраслей промышленности. Эта технология обладает огромным потенциалом для создания новых материалов и технологических процессов, которые позволят нам решать сложные задачи, стоящие перед человечеством.
Я с оптимизмом смотрю в будущее порошковой металлургии и верю, что нас ждут ещё много интересных открытий и достижений!
Заключение
В этой статье я поделился своим практическим опытом применения порошковой металлургии для решения нестандартных задач. Мы рассмотрели кейсы из разных отраслей промышленности и убедились, что эта технология позволяет добиться впечатляющих результатов:
- создавать изделия с уникальными эксплуатационными характеристиками;
- снижать вес и повышать прочность конструкций;
- увеличивать ресурс и надёжность оборудования;
- сокращать затраты на производство и обслуживание.
Я призываю всех, кто работает в сфере металлообработки, не бояться экспериментировать и искать новые пути применения порошковой металлургии.