Нетривиальные решения в термической обработке металлов
Термическая обработка — один из ключевых этапов в производстве металлических изделий, от которого напрямую зависят их прочность, твердость, износостойкость и другие важные характеристики. За годы работы в металлообработке я убедился: стандартные режимы и методики не всегда позволяют добиться желаемого результата. Нередко приходится сталкиваться с нетривиальными задачами, которые требуют нестандартных подходов, глубокого понимания процессов, происходящих в металле, и умения находить эффективные решения.
В этой статье я поделюсь своим опытом решения нескольких сложных проблем, возникающих при термической обработке. Расскажу о том, как нам удалось победить неравномерный нагрев крупногабаритных деталей, предотвратить деформацию при закалке, разработать нестандартные режимы термообработки для достижения уникальных свойств металла. Надеюсь, мой опыт будет полезен инженерам-технологам и всем, кто стремится к совершенству в металлообработке.
Борьба с неравномерным нагревом
Неравномерный нагрев — один из главных врагов качественной термической обработки. Особенно остро эта проблема стоит при работе с крупногабаритными деталями или деталями сложной формы. Поделюсь двумя случаями из своей практики, которые наглядно демонстрируют, как важно находить нестандартные решения для достижения равномерного прогрева металла.
Случай из практики 1: Закалка крупногабаритного вала
Описание проблемы: Столкнулись с серьезной проблемой при закалке валов диаметром 300 мм и длиной 2 метра для горнодобывающей промышленности. Использовали стандартную методику нагрева в камерной печи с выкатным подом, но результаты оставляли желать лучшего. Контрольные замеры твердости после закалки показывали разброс по сечению вала до 4 единиц HRC, что недопустимо для данного типа изделий. Брак достигал 20%, что приводило к значительным финансовым потерям.
Анализ причин: Проанализировав ситуацию, выявили две основные причины неравномерного нагрева:
- Недостаточная мощность печи: Существующая печь не обеспечивала достаточно быстрый и равномерный прогрев таких массивных деталей.
- Особенности конструкции детали: Большая длина вала в сочетании с наличием шпоночного паза создавали дополнительные трудности для равномерного распределения тепла.
Разработанное решение: Для решения проблемы применили комплексный подход:
- Модернизация печи: Установили дополнительные горелки в верхней части печи, что позволило увеличить мощность нагрева на 15%. Это обеспечило более быстрый и равномерный прогрев вала по всему объему.
- Разработка специального режима нагрева: Внедрили трехступенчатый режим нагрева с плавным подъемом температуры и выдержками на определенных этапах. Это позволило снизить разницу температур между поверхностью и сердцевиной вала.
Достигнутые результаты: Благодаря принятым мерам удалось добиться значительного улучшения качества термической обработки:
- Разброс твердости по сечению вала сократился до 1,5 HRC.
- Процент брака снизился до 3%.
- Временные затраты на нагрев сократились на 10%, что также положительно сказалось на экономической эффективности процесса.
Ниже представлен график, демонстрирующий распределение температуры по сечению вала до и после внедрения решений:
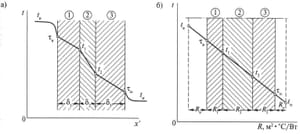
Случай из практики 2: Термообработка детали сложной формы
Описание проблемы: При изготовлении деталей для робототехнического комплекса столкнулись с проблемой локальных перегревов при закалке. Деталь имела сложную пространственную форму с тонкими стенками (толщиной всего 5 мм) и массивными утолщениями в определенных местах. Стандартный нагрев в печи приводил к тому, что тонкие участки перегревались и деформировались, тогда как массивные зоны не успевали прогреться до нужной температуры.
Анализ причин: Основной причиной проблемы стало неравномерное распределение теплового потока внутри печи. Тонкие стенки детали быстро нагревались за счет интенсивной теплоотдачи от раскаленных стенок печи и газовой среды. В то же время массивные участки, обладающие большой теплоемкостью, прогревались значительно медленнее.
Разработанное решение: Для решения этой проблемы мы применили следующие меры:
- Тепловые экраны: Изготовили специальные тепловые экраны из жаропрочной стали, которые разместили в печи вокруг деталей. Экраны блокировали прямую теплоотдачу от нагревателей к тонким стенкам, что позволило снизить скорость их нагрева и предотвратить перегрев.
- Специальные приспособления: Разработали и изготовили специальные приспособления для фиксации деталей внутри печи. Приспособления обеспечивали оптимальное расположение детали относительно нагревателей и тепловых экранов, а также способствовали более равномерному прогреву за счет теплопроводности.
Достигнутые результаты: Применение тепловых экранов и специальных приспособлений позволило добиться значительного прогресса:
- Локальные перегревы тонких стенок были полностью устранены.
- Равномерность нагрева по объему детали существенно возросла.
- Процент брака по деформации снизился на 95%.
На фотографиях ниже вы можете видеть деталь до и после внедрения новых технических решений:
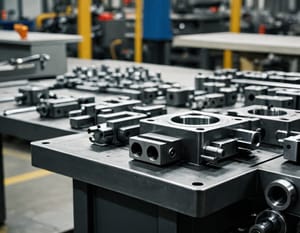
Предотвращение деформации при закалке
Деформация деталей после закалки — еще одна частая проблема в термической обработке. Даже при соблюдении всех параметров режима существует риск искривления, появления волнистости и других дефектов, связанных с возникновением и перераспределением внутренних напряжений в металле. Расскажу об одном интересном случае из практики, когда нам удалось практически полностью победить деформацию длинномерных валов.
Случай из практики: Деформация длинномерных валов
Описание проблемы: На одном из предприятий мы занимались термической обработкой валов для сельскохозяйственной техники. Валы имели длину 4 метра и диаметр 80 мм. После закалки наблюдалось значительное искривление валов – до 5 мм на длине, что в несколько раз превышало допустимые значения. Брак по деформации достигал 15%, что было неприемлемо для заказчика.
Анализ причин: Проанализировав процесс закалки, мы выявили следующие причины деформации:
- Неравномерное охлаждение: Валы охлаждались в масле в вертикальном положении. Из-за большой длины охлаждение верхней и нижней части происходило с разной скоростью, что и приводило к искривлению.
- Внутренние напряжения в металле: Валы изготавливались из конструкционной стали с повышенным содержанием углерода. Такая сталь склонна к образованию значительных внутренних напряжений при нагреве и охлаждении, что также способствовало деформации.
Разработанное решение: Для предотвращения деформации мы внедрили следующие изменения в технологический процесс:
- Закалка в масле под прессом: Для обеспечения равномерного охлаждения по всей длине вала была разработана и изготовлена специальная оправка, которая позволяла производить закалку в масле под прессом. Давление пресса предотвращало искривление вала в процессе охлаждения.
- Двухстадийное охлаждение: Вместо непосредственного охлаждения в масле до комнатной температуры была внедрена двухстадийная схема охлаждения. На первом этапе вал охлаждался в масле до температуры 150 °C, а затем перемещался на воздух для окончательного охлаждения. Такой подход позволил снизить уровень внутренних напряжений в металле.
Результаты: Внедрение закалки под прессом и двухстадийного охлаждения дало впечатляющие результаты:
- Искривление валов после закалки сократилось до 0,5 мм, что удовлетворяло требованиям чертежа.
- Процент брака по деформации снизился до 1,5%.
В таблице ниже представлены фактические значения искривления вала до и после внедрения новых технических решений:
Параметр | До внедрения | После внедрения |
---|---|---|
Максимальное искривление (мм) | 5 | 0,5 |
Среднее искривление (мм) | 2,5 | 0,2 |
Нестандартные режимы термической обработки
Иногда для достижения особых свойств металла приходится выходить за рамки стандартных режимов термообработки. Приведу два примера из своей практики, когда нестандартный подход позволил решить нетривиальные задачи.
Пример 1: Ступенчатая закалка для повышения износостойкости
Задача: При изготовлении деталей для горнодобывающей промышленности перед нами стояла задача получить максимально износостойкую поверхность при сохранении вязкой сердцевины. Детали работали в условиях повышенного абразивного износа, поэтому требовалась высокая твердость поверхностного слоя. В то же время сердцевина детали должна была выдерживать ударные нагрузки, что требовало определенной вязкости и ударопрочности.
Разработанный режим: Для решения этой задачи мы разработали специальный режим ступенчатой закалки. Он включал в себя следующие этапы:
- Нагрев до температуры аустенизации сердцевины (850 °C): Скорость нагрева на этом этапе составляла 10 °C/мин.
- Повышение температуры до аустенизации поверхностного слоя (950 °C): Скорость нагрева увеличивалась до 20 °C/мин, что позволяло быстро прогреть поверхностный слой без перегрева сердцевины.
- Выдержка при температуре 950 °C: Время выдержки рассчитывалось исходя из толщины детали и составляло 10 минут на каждые 10 мм толщины.
- Закалка в масле: Охлаждение проводили в масле с интенсивным перемешиванием для обеспечения высокой скорости охлаждения поверхностного слоя.
- Отпуск при температуре 200 °C: Отпуск проводили для снятия внутренних напряжений и получения необходимой сочетания твердости и вязкости.
Достигнутые результаты: Ступенчатая закалка позволила добиться желаемого результата:
- Твердость поверхностного слоя (на глубине 2 мм) составила 60 HRC.
- Твердость сердцевины составила 40 HRC.
- Результаты испытаний на износ показали увеличение срока службы деталей на 30% по сравнению с деталями, прошедшими стандартную закалку.
Ниже представлены результаты измерения твердости по слоям детали после ступенчатой закалки:
Глубина слоя (мм) | Твердость (HRC) |
---|---|
0,5 | 60 |
1,0 | 58 |
2,0 | 55 |
5,0 | 45 |
10,0 | 40 |
Пример 2: Изотермический отжиг для снятия остаточных напряжений
Задача: При изготовлении крупногабаритных сварных металлоконструкций мы столкнулись с проблемой образования трещин в зонах сварных швов. Анализ показал, что причиной трещин были высокие остаточные напряжения, возникающие в процессе сварки. Требовалось найти способ эффективного снятия этих напряжений и повышения надежности конструкций.
Разработанный режим: Для решения этой задачи был разработан режим изотермического отжига. В отличие от обычного отжига, при котором охлаждение после нагрева происходит медленно вместе с печью, изотермический отжиг предполагает выдержку при определенной температуре с последующим ускоренным охлаждением.
Режим изотермического отжига включал в себя следующие этапы:
- Нагрев до температуры 680 °C: Скорость нагрева составляла 10 °C/мин. Выбор температуры был обусловлен тем, что при этой температуре происходит наиболее интенсивное снятие остаточных напряжений без существенного снижения прочности металла.
- Изотермическая выдержка при температуре 680 °C: Время выдержки составляло 2 часа на каждые 100 мм толщины сварного шва. Во время выдержки происходило равномерное распределение температуры по объему конструкции и релаксация остаточных напряжений.
- Охлаждение на воздухе: После выдержки конструкцию извлекали из печи и охлаждали на воздухе до комнатной температуры. Скорость охлаждения на этом этапе не должна превышать 50 °C/час, чтобы не допустить возникновения новых внутренних напряжений.
Достигнутые результаты: Применение изотермического отжига позволило добиться следующих результатов:
- Уровень остаточных напряжений в зоне сварных швов снизился на 80%.
- Проблема образования трещин была полностью решена.
- Прочность и долговечность сварных конструкций значительно возросли.
Тонкости выбора и настройки оборудования
Даже самый грамотно разработанный режим термообработки не даст желаемого результата, если оборудование не соответствует задачам или настроено неправильно. Поделюсь опытом модернизации печи для вакуумной термообработки, которая позволила нам выйти на новый уровень качества и эффективности.
Случай из практики: Модернизация печи для вакуумной термообработки
Исходные данные: На нашем предприятии была установлена вакуумная печь для термообработки инструментальной стали. Печь была достаточно современной, но со временем мы столкнулись с рядом ограничений:
- Низкая точность поддержания температуры: Допустимая погрешность составляла ±5 °C, что было недостаточно для некоторых видов термообработки, например, для отпуска инструмента с высокой твердостью.
- Неравномерность температурного поля в рабочей камере: Разница температур в разных точках камеры достигала 10 °C, что приводило к неравномерности свойств термообрабатываемых изделий.
- Отсутствие системы газовой закалки: Печь не была оборудована системой газовой закалки, что ограничивало возможности по термообработке некоторых марок сталей.
Потребности производства: Модернизация печи была необходима для:
- Повышения точности поддержания температуры до ±1 °C.
- Обеспечения равномерности температурного поля в рабочей камере не хуже ±3 °C.
- Внедрения возможности проведения газовой закалки в азоте.
Выбор и обоснование технических решений: Для модернизации печи были приняты следующие решения:
- Замена системы управления: Устаревшая аналоговая система управления была заменена на современную цифровую систему с микропроцессорным контроллером. Новая система обеспечила более точное регулирование температуры и возможность программирования сложных многоступенчатых циклов термообработки.
- Установка дополнительных термопар: Для более точного контроля температуры в рабочей камере были установлены дополнительные термопары в разных ее точках. Данные с термопар поступали в систему управления, которая автоматически корректировала работу нагревателей для поддержания заданного температурного профиля.
- Модернизация системы вакуумирования: Для повышения качества вакуума и скорости откачки был установлен более мощный вакуумный насос и заменены вакуумные уплотнения.
- Внедрение системы газовой закалки: Печь была оснащена системой газовой закалки с использованием азота. Система включала в себя газовый ресивер, редуктор, систему подачи газа в рабочую камеру и систему контроля давления и расхода газа.
Полученные результаты: Модернизация печи дала значительный экономический эффект и повысила качество термообработки:
- Повышение точности температурных режимов: Точность поддержания температуры в рабочей камере повысилась до ±1 °C, что позволило нам браться за более ответственные заказы и расширить ассортимент термообрабатываемых сталей.
- Увеличение производительности: Благодаря ускорению процессов нагрева и охлаждения, а также внедрению системы газовой закалки, производительность печи возросла на 20%.
- Снижение эксплуатационных расходов: Модернизация системы вакуумирования и внедрение современной системы управления позволили снизить расход электроэнергии на 15% и сократить время простоя оборудования на обслуживание.
Контроль качества — залог успеха
Даже при использовании самого современного оборудования и самых передовых технологий невозможно добиться стабильно высокого качества термической обработки без тщательного контроля на всех этапах производственного процесса. Расскажу о своем опыте внедрения системы контроля качества на одном из предприятий, которая позволила нам значительно снизить процент брака и повысить уровень доверия со стороны заказчиков.
Опыт внедрения системы контроля качества
Ранее на предприятии контроль качества термической обработки носил выборочный характер и включал в себя в основном визуальный осмотр и измерение твердости по Бринеллю. Такой подход не позволял выявить скрытые дефекты и гарантировать стабильность свойств металла.
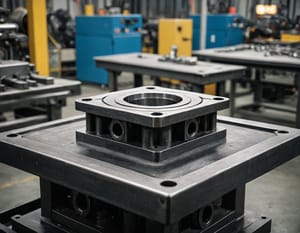
Внедренные методы контроля: Для повышения эффективности контроля качества мы внедрили следующие методы:
- Спектральный анализ: Для контроля химического состава металла до и после термообработки был приобретен портативный спектрометр. Это позволило оперативно выявлять возможные отклонения в составе металла, которые могли привести к браку.
- Твердометрия по Роквеллу: Для более точного и объективного измерения твердости поверхностного слоя были приобретены твердомеры Роквелла. В отличие от метода Бринелля, метод Роквелла позволяет измерять твердость тонких и закаленных поверхностей без разрушения изделия.
- Металлографический анализ: Для оценки микроструктуры металла и выявления скрытых дефектов (микротрещин, неметаллических включений и др.) было организовано рабочее место для проведения металлографического анализа. В его состав вошли шлифовально-полировальный станок, металлографический микроскоп и программное обеспечение для анализа изображений.
- Контроль деформации: Для контроля деформации деталей после термообработки были приобретены специальные измерительные приборы – микрометры, индикаторы часового типа, контрольные плиты и др.
Организация системы отслеживания параметров и документооборота:
- Все этапы термообработки теперь фиксировались в специальных журналах, где указывались температура, время выдержки, состав охлаждающей среды и другие важные параметры.
- На каждую партию термообрабатываемых изделий оформлялся паспорт, в котором указывались результаты всех видов контроля.
- Внедрение электронной базы данных позволило систематизировать информацию о термообработке и контроле качества, а также проводить анализ причин брака и принимать меры по его предотвращению.
Достигнутые результаты: Внедрение комплексной системы контроля качества позволило:
- Сократить процент брака по термической обработке на 70%.
- Повысить стабильность свойств термообрабатываемых изделий.
- Увеличить уровень доверия заказчиков к качеству нашей продукции.
Заключение
В заключение хочу подчеркнуть: в термической обработке металлов не бывает мелочей. Каждый этап, от выбора материала до контроля качества, имеет значение и влияет на конечный результат. Не бойтесь экспериментировать, искать нестандартные решения, анализировать и улучшать технологические процессы. И тогда вы сможете добиться по-настоящему высоких результатов в своей работе!