Нюансы плазменной резки различных металлов
Плазменная резка, несмотря на свою универсальность, предъявляет особые требования к выбору режимов при работе с определенными материалами. Сложнообрабатываемые марки стали, такие как высокоуглеродистые или легированные, требуют от оператора не только знания общих принципов плазменной резки, но и понимания нюансов поведения металла в условиях высоких температур.
Резка сложнообрабатываемых марок стали
Резка сталей с высоким содержанием углерода
Высокоуглеродистые стали обладают повышенной склонностью к закалке, что может привести к образованию твердых и хрупких структур в зоне термического воздействия плазменной дуги. Для предотвращения этого нежелательного эффекта необходимо снизить тепловую нагруженность материала в процессе резки.
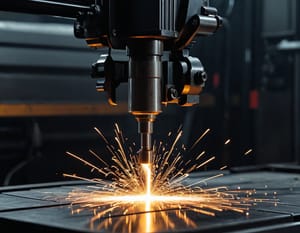
Практические рекомендации:
- Уменьшение силы тока на 15-20% по сравнению с резкой низкоуглеродистых сталей аналогичной толщины.
- Увеличение скорости резки на 10-15% для сокращения времени воздействия высокой температуры на металл.
- Использование защитных газов с повышенным содержанием азота, что способствует охлаждению зоны реза и снижает риск закаливания.
Как правило, формула для расчета скорости резки стали имеет вид:
V = k * I / h
где:
- V - скорость резки, м/мин
- k - коэффициент, зависящий от марки стали и типа плазмотрона (обычно указывается в паспорте оборудования)
- I - сила тока, А
- h - толщина металла, мм
При резке высокоуглеродистых сталей коэффициент "k" следует уменьшать на 10-15% для компенсации повышенной склонности к закалке.
Резка легированных сталей
Легированные стали, благодаря присутствию в их составе таких элементов, как хром, никель, молибден и другие, обладают повышенной прочностью, жаростойкостью и коррозионной стойкостью. Однако эти же легирующие элементы могут создавать определенные трудности при плазменной резке.
Основные проблемы:
- Перегрев и деформация: Легирующие элементы повышают температуру плавления стали, что может привести к перегреву материала в зоне реза и его последующей деформации.
- Образование окалины: Некоторые легирующие элементы, такие как хром, способствуют образованию плотной и тугоплавкой окалины, которая затрудняет процесс резки и снижает качество кромки.
Рекомендации по выбору режимов резки:
- Снижение силы тока на 5-10% по сравнению с резкой низколегированных сталей аналогичной толщины.
- Увеличение скорости резки на 10-20% для минимизации времени воздействия высокой температуры.
- Использование кислорода в качестве плазмообразующего газа для интенсификации процесса горения и уменьшения образования окалины (особенно актуально для сталей с высоким содержанием хрома).
- Применение специальных сопел и электродов с повышенной стойкостью к высоким температурам и агрессивным средам.
Пример из практики:
При резке толстолистовой конструкционной стали марки 09Г2С толщиной 20 мм на плазморежущем станке с ЧПУ возникла проблема деформации листов в зоне реза. Анализ ситуации показал, что стандартные режимы резки, рекомендованные производителем оборудования, не учитывали специфику данной марки стали.
Решение:
- Была проведена серия экспериментальных резов с постепенным снижением силы тока и увеличением скорости резки.
- В результате были найдены оптимальные режимы, которые позволили минимизировать деформацию листов без потери качества реза.
- Сила тока была снижена на 15%, а скорость резки увеличена на 20%.
- Дополнительно было применено специальное сопло с увеличенным ресурсом работы, что позволило сократить количество перерывов на замену расходных материалов.
Формулы для расчета параметров резки
При работе с легированными сталями базовые формулы для расчета параметров резки требуют корректировки с учетом влияния легирующих элементов. Например, для приблизительного расчета силы тока (I) с учетом легирующих элементов можно использовать следующую формулу:
I = (h * K * (1 + 0.004 * C + 0.003 * Mn + 0.001 * (Cr + Ni + Mo))) / (η * cos α)
где:
- I - сила тока, A
- h - толщина металла, мм
- K - коэффициент, зависящий от марки стали, типа плазмотрона и состава плазмообразующего газа (обычно указывается в документации к оборудованию)
- C, Mn, Cr, Ni, Mo - содержание углерода, марганца, хрома, никеля и молибдена в стали, % соответственно
- η - КПД плазмотрона
- α - угол реза (обычно равен 90 градусам, cos 90° = 0)
Таблица: Рекомендации по выбору защитных газов для резки разных марок сталей:
Марка стали | Толщина, мм | Защитный газ | Комментарий |
---|---|---|---|
Ст3сп | До 10 | Воздух | Оптимальный вариант для неответственных деталей |
Ст3сп | 10-20 | Азот | Улучшает качество кромки, снижает окалину |
Ст20 | До 20 | Воздух | Стандартный выбор для конструкционных сталей |
Ст20 | Свыше 20 | Азот | Повышает качество реза, снижает деформацию |
09Г2С | До 30 | Азот-кислородная смесь | Снижает окалину, улучшает качество кромки |
12Х18Н10Т | До 10 | Азот-аргоновая смесь | Предотвращает окисление хрома, минимизирует деформацию |
12Х18Н10Т | 10-20 | Аргон | Обеспечивает максимальное качество реза и минимум окалины |
Важно помнить, что данные формулы и рекомендации носят оценочный характер. Оптимальные режимы резки для конкретной марки стали и оборудования следует подбирать экспериментальным путем, проводя пробные резы и анализируя их результаты.
Проблемы и решения при плазменной резке алюминия
Алюминий и его сплавы, благодаря сочетанию легкости, прочности и коррозионной стойкости, являются востребованным материалом во многих отраслях. Однако плазменная резка этого металла требует от технолога особого внимания и знания ряда нюансов.
Одна из особенностей алюминия - его высокая теплопроводность. Алюминий чрезвычайно эффективно рассеивает тепло, что, с одной стороны, делает его ценным материалом для изготовления радиаторов и теплообменников, а с другой - создает трудности при плазменной резке. Тепло от плазменной дуги быстро распространяется по всей площади листа, не успевая сформировать узкую зону локального нагрева, необходимую для эффективного плавления и удаления металла. Это может приводить к нестабильности горения дуги, образованию неровной, рваной кромки реза, а также к увеличению тепловой нагрузки на оборудование. Для компенсации высокой теплопроводности алюминия необходимо увеличивать силу тока плазменной дуги на 10-20% по сравнению с резкой стали аналогичной толщины. Высокая скорость резки также способствует уменьшению зоны теплового воздействия и минимизирует риск деформации материала.
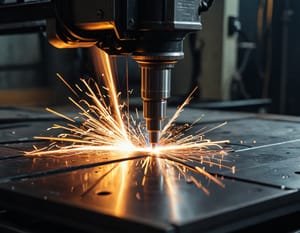
Еще одна проблема - образование на поверхности алюминия стойкой оксидной пленки (Al2O3). Эта пленка, обладающая высокой температурой плавления, препятствует равномерному проплавлению металла плазменной дугой. В результате на кромке реза могут образовываться наплывы и неровности, а также происходить налипание брызг расплавленного металла на поверхность обрабатываемой детали. Для борьбы с оксидной пленкой используют плазмообразующие газы с высокой теплопроводностью, такие как аргон или азот. Они обеспечивают более высокую температуру дуги и способствуют более эффективному плавлению оксидной пленки. Кроме того, в состав плазмообразующего газа могут вводиться специальные компоненты, например, водород (H2) или смеси на основе азота и водяного пара. Водород, вступая в реакцию с оксидом алюминия, образует летучие соединения, которые легко удаляются из зоны реза.
Особое внимание следует уделять резке алюминиевых сплавов с высоким содержанием магния. Магний – ценный легирующий элемент, повышающий прочность и коррозионную стойкость алюминия. Однако он обладает свойством легко воспламеняться и гореть при высоких температурах, что создает дополнительные трудности при плазменной резке. При неправильно выбранных режимах резки магний может выгорать из расплава, что приводит к ухудшению механических свойств материала в зоне реза. Кроме того, выгорание магния может сопровождаться выделением большого количества тепла и образованием яркого ослепительного пламени, что небезопасно для оператора.
Для предотвращения выгорания магния и обеспечения высокого качества реза рекомендуется использовать инертные газы, такие как аргон, в качестве плазмообразующего и защитного газа. Аргон не вступает в химические реакции с расплавленным металлом и создает вокруг зоны реза инертную атмосферу, препятствующую окислению и выгоранию магния. Важную роль играет и скорость резки – ее увеличивают для сокращения времени воздействия высокой температуры на металл.
Пример из практики: на одном из предприятий, где я работал, потребовалось изготовить партию деталей из алюминиевого сплава АМг6, содержащего около 6% магния. При резке по стандартной технологии, рекомендованной для алюминия, наблюдалось сильное выгорание магния, кромка реза была покрыта слоем белого оксида магния, а сами детали деформировались от перегрева. Проблему удалось решить, полностью заменив сжатый воздух на аргон в системе плазменной резки. Это позволило стабилизировать процесс резки, исключить выгорание магния и получить детали требуемого качества.
Еще одна важная особенность плазменной резки алюминия – необходимость учитывать тепловое расширение материала. Алюминий обладает высоким коэффициентом теплового расширения, что может приводить к деформации деталей, особенно при резке тонколистового материала или вырезании сложных контуров. Для минимизации деформаций важно обеспечить эффективный отвод тепла из зоны реза и предотвратить перегрев материала.
Вот несколько рекомендаций, которые помогают снизить риск деформаций:
- Увеличение скорости резки: Чем быстрее происходит резка, тем меньше времени на нагрев материала и тем ниже вероятность его деформации.
- Использование системы охлаждения: При резке алюминия большой толщины или при высоких токах резки эффективным способом предотвратить перегрев материала является применение специальных систем охлаждения. Они подают охлаждающую жидкость непосредственно в зону реза, снижая температуру материала и предотвращая его деформацию.
- Оптимизация геометрии реза: При вырезании сложных контуров важно правильно выбирать направление резки, чтобы минимизировать накопление тепла в определенных зонах материала и снизить риск деформаций.
Расчет необходимого объема охлаждения при резке алюминия большой толщины проводят, исходя из мощности плазменной дуги, скорости резки, теплофизических свойств материала и других факторов. Существуют специализированные программы, которые помогают технологам рассчитать оптимальные параметры охлаждения для конкретных условий резки.
В следующем разделе мы рассмотрим тонкости плазменной резки других "капризных" металлов, таких как медь и титан.
Тонкости работы с "капризными" металлами
Помимо стали и алюминия, плазменная резка находит применение и для обработки других, более "капризных" металлов, каждый из которых имеет свои особенности и требует индивидуального подхода.
Резка меди
Медь – материал с высокой теплопроводностью и склонностью к окислению при нагревании. При плазменной резке меди важно обеспечить быстрый отвод тепла из зоны реза, чтобы предотвратить перегрев и деформацию материала. Для этого используют высокие скорости резки и эффективные системы охлаждения.
Основные проблемы при резке меди:
- Окисление: При высоких температурах медь активно взаимодействует с кислородом, образуя на поверхности оксидную пленку. Эта пленка ухудшает качество реза, делая его неровным и рваным.
- Липкость расплава: Расплавленная медь обладает высокой вязкостью, что может приводить к налипанию брызг металла на поверхность реза и образованию дефектов.
Рекомендации по выбору режимов резки меди:
- Использование азота в качестве плазмообразующего газа для минимизации окисления.
- Применение специальных сопел с удлиненным каналом, что способствует более концентрированному потоку плазмы и уменьшает зону теплового воздействия.
- Регулярная замена расходных материалов, так как при резке меди они износятся быстрее, чем при резке стали или алюминия.
Резка титана
Титан и его сплавы, обладая исключительной прочностью и коррозионной стойкостью в сочетании с относительно небольшим весом, завоевали прочные позиции в авиастроении, ракетостроении и других высокотехнологичных отраслях. Однако обработка этих металлов, включая плазменную резку, сопряжена с рядом трудностей, обусловленных их уникальными физико-химическими свойствами.
Титан при высоких температурах чрезвычайно активно взаимодействует с кислородом, азотом и другими газами, присутствующими в воздухе. Это приводит к интенсивному окислению и нитридообразованию в зоне реза, что негативно сказывается на качестве кромки и может приводить к ухудшению механических свойств материала.
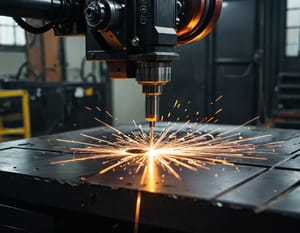
Для минимизации негативного влияния атмосферных газов плазменную резку титана проводят с применением инертных газов высокой чистоты, таких как аргон и гелий, как в качестве плазмообразующей среды, так и для защиты зоны реза. Особое внимание уделяют выбору расходных материалов для плазмотрона – сопел и электродов.
Материал сопла/электрода | Преимущества | Недостатки |
---|---|---|
Гафний | Высокая стойкость к износу при работе с титаном | Высокая стоимость |
Цирконий | Хорошая стойкость к окислению | Менее долговечны, чем гафниевые |
Медь с гафниевым покрытием | Оптимальное соотношение цены и качества | Требуют более частой замены, чем гафниевые |
Выбор конкретного типа сопел и электродов зависит от ряда факторов: толщины резаемого материала, требуемого качества кромки, интенсивности эксплуатации оборудования и бюджета проекта.
Из своего опыта могу сказать, что продлить срок службы расходных материалов при плазменной резке меди и титана помогают следующие приемы:
- Тщательная подготовка поверхности металла перед резкой. Удаление с поверхности листов окалины, ржавчины, масляных пятен и других загрязнений позволяет снизить риск повреждения сопла и электрода брызгами расплавленного металла и продуктами горения.
- Контроль зазора между соплом и поверхностью материала. Слишком большой зазор приводит к рассеиванию плазменной дуги и перегреву сопла, а слишком маленький – к риску столкновения сопла с материалом и его повреждению.
- Охлаждение плазмотрона. Использование эффективной системы охлаждения плазмотрона позволяет снизить температуру сопла и электрода и увеличить их ресурс.
В следующем разделе мы рассмотрим общие принципы оптимизации процесса плазменной резки для повышения ее эффективности и качества.
Оптимизация процесса плазменной резки для повышения эффективности
Плазменная резка — гибкий и универсальный способ обработки металлов, однако для достижения максимальной эффективности и качества реза важно не только знать особенности работы с разными материалами, но и уметь тонко настраивать параметры процесса и применять современное оборудование.
Тонкая настройка параметров резки:
Каждая задача по плазменной резке уникальна и требует индивидуального подхода к выбору режимов. Не существует универсального набора параметров, которые гарантировали бы оптимальный результат во всех случаях.
Основные параметры, которые подлежат регулировке:
- Сила тока: Влияет на толщину резаемого металла и скорость резки. Увеличение силы тока позволяет резать более толстые листы, но при этом возрастает ширина реза и увеличивается тепловое воздействие на материал.
- Скорость резки: Влияет на ширину реза и качество кромки. Высокая скорость резки обеспечивает узкий рез и минимизирует тепловое воздействие на материал, но при этом снижается качество кромки и увеличивается риск непрореза.
- Расстояние между соплом и материалом: Влияет на форму дуги и качество реза. Оптимальное расстояние зависит от типа плазмотрона, силы тока и других факторов.
- Состав и расход плазмообразующего и защитного газа: Влияют на стабильность дуги, качество кромки, скорость резки и тепловое воздействие на материал.
Часто технологам приходится искать компромисс между двумя противоречивыми требованиями: максимальная скорость резки и идеальное качество кромки. Высокая скорость важна для повышения производительности, но при этом может страдать качество кромки – она становится менее гладкой и требует дополнительной обработки. С другой стороны, получение идеально ровной и чистой кромки позволяет сэкономить время и ресурсы на последующей механической обработке, но требует снижения скорости резки.
Для нахождения оптимального баланса между скоростью и качеством реза проводят серию тестовых резов с разными параметрами и анализируют полученные результаты. Современные системы ЧПУ для плазменной резки позволяют сохранять в памяти несколько наборов параметров для разных материалов и толщин, что значительно упрощает работу технолога.
Автоматизация процесса резки
Внедрение систем числового программного управления (ЧПУ) в оборудование для плазменной резки привело к настоящей революции в этой области. Если раньше плазменная резка была преимущественно ручным трудоемким процессом, то сегодня она становится все более автоматизированной и высокоточной.
Возможности ЧПУ плазменной резки:
- Высокая точность и повторяемость реза. Системы ЧПУ позволяют выдерживать заданные параметры резки с точностью до сотых долей миллиметра, что особенно важно при изготовлении деталей сложной формы и высокой точности.
- Возможность резки по сложным траекториям. С помощью ЧПУ можно легко программировать резку по любым криволинейным контурам, что практически невозможно реализовать при ручной резке.
- Автоматический контроль параметров резки. Системы ЧПУ могут автоматически поддерживать оптимальные параметры резки в зависимости от типа материала, его толщины и других факторов.
- Повышение производительности и снижение влияния человеческого фактора. Автоматизация процесса резки позволяет значительно сократить время обработки деталей и минимизировать риск брака, связанного с ошибками оператора.
Пример из практики: На одном из предприятий, где я внедрял системы автоматизации, стояла задача повысить точность и производительность резки крупногабаритных листов стали для изготовления металлоконструкций. Использовавшаяся ранее установка ручной плазменной резки не позволяла добиться требуемой точности, а сам процесс резки занимал много времени и был чрезвычайно трудоемким.
После анализа производственных потребностей было принято решение о внедрении портальной машины плазменной резки с ЧПУ. Это позволило не только автоматизировать процесс резки, но и значительно повысить его точность и скорость. Время резки одной детали сократилось в несколько раз, а количество брака, связанного с человеческим фактором, практически свелось к нулю.
Важным этапом внедрения стало обучение персонала работе на новом оборудовании и программированию ЧПУ. В результате предприятие получило мощный инструмент для высокоточной и эффективной резки металла, который позволил расширить производственные возможности и повысить конкурентоспособность на рынке.
Заключение
Плазменная резка — эффективный и универсальный метод обработки металлов, который, при правильном подходе, позволяет достигать высокой точности, качества и производительности. Однако для раскрытия всего потенциала этой технологии необходимо не только современное оборудование, но и глубокое понимание физики процесса, специфики работы с различными материалами и нюансов настройки режимов резки.
Надеюсь, что информация, которой я поделился в этой статье, окажется полезной для вас и поможет вам достичь новых высот в области металлообработки.