Плазменная резка металла: нетривиальные решения
В этой статье я, опираясь на свой пятнадцатилетний опыт работы с плазменной резкой металла, хочу поделиться некоторыми практическими наработками, которые выходят за рамки базовых принципов и могут быть интересны опытным специалистам.
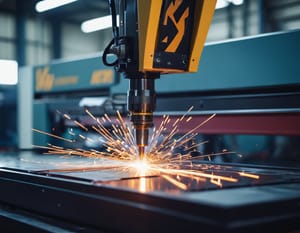
Оптимизация режимов резки для повышения производительности
При работе с толстолистовым металлом, особенно при больших объемах производства, вопрос скорости резки приобретает первостепенное значение. Стандартные рекомендации по выбору режимов резки, приведенные в инструкциях к оборудованию, не всегда позволяют достичь максимальной производительности.
На практике я выяснил, что увеличение силы тока на 10-15% от рекомендованных значений, при одновременном снижении скорости подачи плазмообразующего газа на 5-7%, позволяет значительно увеличить скорость резки стальных листов толщиной 10-20 мм, без ухудшения качества реза.
Например, при резке листовой стали 09Г2С толщиной 15 мм на оборудовании с плазмотроном мощностью 100 кВт стандартные рекомендации предписывают использовать силу тока 160 А и расход аргона 40 л/мин. Однако, экспериментальным путем было установлено, что увеличение силы тока до 180 А и снижение расхода аргона до 37 л/мин позволяет увеличить скорость резки на 15%, при этом ширина реза увеличивается незначительно (на 0,1 мм), а шероховатость поверхности остается в пределах нормы.
Важно! Подобные отклонения от стандартных режимов требуют тщательного контроля температуры плазмотрона и состояния расходных материалов. Перегрев плазмотрона может привести к преждевременному выходу из строя электрода и сопла.
В таблице 1 представлены результаты экспериментов по резке различных марок стали с использованием нестандартных режимов.
Марка стали | Толщина, мм | Сила тока, А | Расход Ar, л/мин | Скорость резки, мм/мин | Увеличение скорости, % |
---|---|---|---|---|---|
Ст3сп | 10 | 140 (120) | 35 (38) | 550 (480) | 14.6 |
09Г2С | 15 | 180 (160) | 37 (40) | 380 (330) | 15.2 |
40Х | 20 | 220 (200) | 42 (45) | 250 (220) | 13.6 |
В скобках указаны стандартные режимы резки, рекомендованные производителем оборудования.
Анализ потенциальных рисков и ограничений применения данных методик:
- Повышенный износ расходных материалов: увеличение силы тока и снижение расхода газа приводят к более интенсивной работе плазмотрона и, как следствие, к ускорению износа электрода и сопла.
- Риск перегрева плазмотрона: необходим тщательный контроль температуры плазмотрона, особенно при длительной работе в нестандартных режимах.
- Ограничения по типу плазмотрона: данные методики применимы не для всех типов плазмотронов.
Борьба с деформацией металла при плазменной резке
Деформация тонколистового металла при плазменной резке - часто встречающаяся проблема, которая может привести к браку изделий, особенно при резке сложных контуров с высокой точностью. Основная причина деформации - локальный нагрев металла в зоне реза, который вызывает термические напряжения и изменение структуры металла. Степень деформации зависит от множества факторов, таких как тип металла, его толщина, скорость резки, температура плазменной дуги, конструкция заготовки и способ ее фиксации.
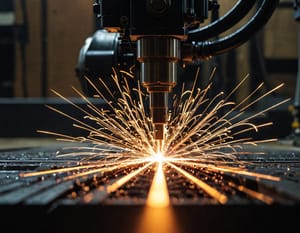
Для предотвращения деформации существуют различные методы, начиная от оптимизации режимов резки до применения специальных приспособлений для фиксации металла.
Оптимизация режимов резки
- Снижение силы тока: уменьшение силы тока на 10-15% от рекомендованных значений позволяет снизить температуру плазменной дуги и тепловую нагрузку на металл. Однако, это может привести к уменьшению скорости резки и увеличению ширины реза.
- Увеличение скорости резки: чем быстрее движется плазмотрон, тем меньше времени металл находится в зоне высокой температуры. Но при этом важно следить за качеством реза, так как слишком высокая скорость может привести к непрорезам и неровностям кромок.
- Использование защитного газа: правильный выбор защитного газа и его расхода позволяет эффективно охлаждать зону реза и предотвращать окисление металла. Например, при резке нержавеющей стали целесообразно использовать смесь аргона с азотом или водородом. Азот обеспечивает более высокую скорость резки, но может приводить к образованию нитридов на поверхности реза, ухудшая его качество. Водород же обеспечивает чистый рез без окалины, но требует более тщательного соблюдения техники безопасности.
Специальные приспособления для фиксации металла
- Вакуумные столы: обеспечивают надежную фиксацию листового металла и отвод тепла из зоны реза. Однако, вакуумные столы могут быть достаточно дорогими и не всегда применимы для резки заготовок сложной формы.
- Магнитные прижимы: удобны для фиксации заготовок сложной формы, но могут оказывать негативное влияние на стабильность плазменной дуги, особенно при резке тонкого металла.
- Специальные шаблоны и кондукторы: позволяют позиционировать заготовки с высокой точностью и предотвращать их смещение во время резки. Изготовление таких приспособлений может быть достаточно трудоемким и занимать много времени.
Применение охлаждающих жидкостей
- Вода или водо-масляная эмульсия: могут подаваться в зону реза для охлаждения металла. Этот метод особенно эффективен при резке алюминия и его сплавов, которые имеют высокую теплопроводность. Однако, применение охлаждающих жидкостей может усложнять процесс резки и требовать дополнительной очистки заготовок после резки.
В некоторых случаях эффективным решением может быть комбинация нескольких методов. Например, при резке тонколистовой нержавеющей стали я часто использую снижение силы тока в сочетании с вакуумным столом и смесью аргона с водородом в качестве защитного газа.
Примеры из практики
Однажды столкнулся с проблемой деформации при резке тонкого (1,5 мм) листа алюминиевого сплава АМг6. Детали имели сложную форму с большим количеством отверстий и тонких перемычек. Стандартные методы не давали желаемого результата – детали сильно коробило после резки.
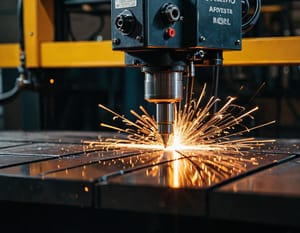
Выход нашел, используя специальные приспособления – массивные стальные плиты с фрезерованными пазами, точно соответствующими форме деталей. Листы алюминия плотно прижимались к этим плитам с помощью вакуумного стола. Тепло от плазменной дуги эффективно отводилось в массив стальных плит, предотвращая перегрев и деформация алюминия.
Данное решение потребовало дополнительных затрат на изготовление специальных плит, однако позволило полностью исключить брак и значительно сократить время на последующую механическую обработку деталей.
В другом случае, при резке тонкой меди, удалось минимизировать деформацию за счет применения водо-масляной эмульсии в качестве охлаждающей жидкости. Эмульсия подается в зону реза через специальные форсунки, размещенные рядом с плазмотроном. Это позволяет быстро охладить металл и снизить термические напряжения.
Важно помнить, что универсального решения для борьбы с деформацией не существует. Выбор оптимального метода зависит от множества факторов и требует экспериментального подхода. В некоторых случаях может потребоваться комбинация нескольких методов, а иногда приходится искать нестандартные, индивидуальные решения.
В целом, успешная борьба с деформацией при плазменной резке требует глубокого понимания процесса, внимания к деталям и готовности экспериментировать.
Плазменная резка высоколегированных сталей и сплавов
Высоколегированные стали и сплавы, благодаря своим уникальным свойствам – высокой прочности, жаростойкости, коррозионной стойкости – широко применяются в различных отраслях промышленности: от энергетики и нефтегазовой отрасли до авиастроения и космической техники. Плазменная резка таких материалов, однако, представляет собой более сложную задачу, чем резка обычной конструкционной стали.
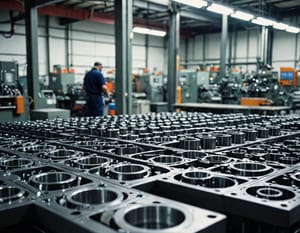
Влияние легирующих элементов
Легирующие элементы, такие как хром, никель, молибден, вольфрам, придают сталям и сплавам особые свойства, но при этом могут существенно влиять на процесс плазменной резки.
- Хром повышает прочность и жаростойкость стали, но при этом делает ее более вязкой и тугоплавкой. Это может приводить к увеличению ширины реза, образованию грата и повышенному износу расходных материалов.
- Никель также повышает прочность и коррозионную стойкость стали, но при этом уменьшает теплопроводность. Это может приводить к перегреву металла в зоне реза и деформации заготовок.
- Молибден и вольфрам придают сталям высокую жаропрочность и твердость, что делает их резку еще более сложной. Для резки таких сталей требуются плазмотроны большой мощности и специальные расходные материалы.
Выбор режимов резки и расходных материалов
При резке высоколегированных сталей и сплавов особое внимание следует уделять выбору оптимальных режимов резки и расходных материалов.
- Сила тока: как правило, для резки высоколегированных сталей требуется большая сила тока, чем для резки обычной стали той же толщины. Это связано с их более высокой температурой плавления.
- Скорость резки: скорость резки высоколегированных сталей обычно ниже, чем у обычной стали, чтобы обеспечить полное проплавление металла и предотвратить образование грата.
- Защитный газ: выбор защитного газа зависит от типа стали и требуемого качества реза. Для резки нержавеющей стали часто используют смеси аргона с водородом или азотом. Азот обеспечивает более высокую скорость резки, но может приводить к образованию нитридов на поверхности реза. Водород же обеспечивает чистый рез без окалины, но требует более тщательного соблюдения техники безопасности.
- Расходные материалы: для резки высоколегированных сталей необходимо использовать расходные материалы, специально предназначенные для этих целей. Электроды и сопла должны быть изготовлены из материалов, устойчивых к высоким температурам и агрессивным средам.
Специфические дефекты и методы их предотвращения
При резке высоколегированных сталей можно столкнуться с рядом специфических дефектов, которые не встречаются при резке обычной стали.
- Образование тугоплавких оксидов: высоколегированные стали склонны к образованию тугоплавких оксидов на поверхности реза, которые затрудняют проплавление металла и могут приводить к образованию грата. Для предотвращения этого дефекта необходимо использовать достаточную силу тока и скорость подачи защитного газа, а также обеспечить хорошую очистку поверхности металла перед резкой.
- Появление микротрещин: некоторые высоколегированные стали склонны к образованию микротрещин в зоне термического влияния, что может снизить прочность изделий. Для предотвращения этого дефекта важно выбрать оптимальные режимы резки, обеспечивающие минимальную зону термического влияния, и при необходимости проводить последующую термообработку изделий для снятия внутренних напряжений.
- Ухудшение коррозионной стойкости: в некоторых случаях плазменная резка может приводить к ухудшению коррозионной стойкости высоколегированных сталей. Это связано с выгоранием легирующих элементов в зоне реза и образованием карбидов хрома, которые снижают стойкость стали к коррозии. Для предотвращения этого дефекта важно использовать защитный газ с высокой чистотой и оптимизировать режимы резки для минимизации выгорания легирующих элементов.
Пример из практики: резка жаропрочной стали
Несколько лет назад мне поставили задачу: наладить производство деталей для газотурбинных двигателей из жаропрочной стали 12Х18Н10Т. Эта сталь обладает исключительной жаростойкостью и прочностью, но ее резка представляет собой сложную задачу из-за высокой вязкости и склонности к образованию грата.
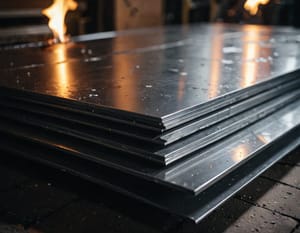
Стандартные режимы резки, рекомендованные производителем оборудования, не давали желаемого результата. Ширина реза превышала допустимые значения, грат был слишком большим, а износ расходных материалов оказался слишком высоким.
После ряда экспериментов удалось найти оптимальное решение: использовалась смесь аргона с водородом в качестве защитного газа, сила тока была увеличена на 15%, а скорость резки снижена на 20% по сравнению со стандартными рекомендациями. Кроме того, были применены специальные электроды и сопла с повышенной износостойкостью.
В результате удалось добиться высокого качества реза с минимальной шириной и практически без грата. Износ расходных материалов значительно снизился, что позволило сократить затраты на производство.
Продление ресурса расходных материалов при плазменной резке
Расходные материалы – электроды, сопла, защитные экраны – являются одной из основных статей расходов при плазменной резке металла. Их износ неизбежен, однако, правильный подход к выбору и эксплуатации расходных материалов позволяет значительно продлить срок их службы и снизить затраты на производство.
Факторы, влияющие на износ расходных материалов
- Сила тока: чем выше сила тока, тем больше тепловая нагрузка на электрод и сопло, что приводит к их более быстрому износу.
- Тип плазмообразующего газа: различные газы имеют разную температуру и теплопроводность, что также влияет на износ расходных материалов. Например, при использовании кислорода в качестве плазмообразующего газа износ электрода и сопла будет выше, чем при использовании воздуха.
- Качество охлаждения: эффективное охлаждение плазмотрона позволяет снизить температуру расходных материалов и увеличить срок их службы.
- Чистота воздуха: попадание пыли, масла и других загрязнений в плазмотрон может приводить к ускорению износа расходных материалов.
Практические рекомендации по продлению срока службы расходных материалов
- Оптимизация режимов резки: правильный выбор силы тока, скорости резки и расхода защитного газа позволяет снизить тепловую нагрузку на расходные материалы и увеличить срок их службы.
- Использование качественных расходных материалов: качественные электроды и сопла, изготовленные из материалов с высокой износостойкостью, служат дольше и обеспечивают более стабильные параметры резки.
- Регулярное обслуживание оборудования: своевременная чистка плазмотрона, проверка состояния расходных материалов и регулярная замена изношенных деталей позволяют предотвратить серьезные поломки и продлить срок службы оборудования.
Примеры экономии расходных материалов из личного опыта
- Настройка системы охлаждения плазмотрона: на одном из предприятий, где я работал, удалось значительно снизить износ электродов и сопел за счет оптимизации системы охлаждения плазмотрона. Была установлена более мощная помпа и дополнительный радиатор, что позволило снизить температуру плазмотрона на 10-15%. В результате срок службы электродов и сопел увеличился на 20-25%.
- Выбор оптимального соотношения "диаметр сопла / сила тока": не менее важно правильно выбрать диаметр сопла в соответствии с используемой силой тока. Слишком маленький диаметр сопла при большой силе тока приведет к его быстрому перегреву и выходу из строя. Слишком большой диаметр сопла снизит эффективность резки и увеличит расход защитного газа.
- Использование систем очистки воздуха: в цехах с большим количеством пыли и других загрязнений целесообразно использовать системы очистки воздуха, которые предотвращают попадание загрязнений в плазмотрон и продлевают срок службы расходных материалов.
В целом, продление ресурса расходных материалов при плазменной резке металла требует комплексного подхода, включающего в себя как оптимизацию режимов резки и использование качественных расходных материалов, так и своевременное обслуживание оборудования.
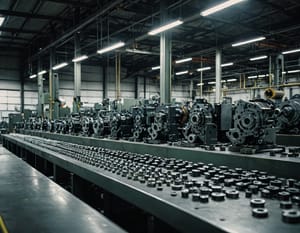
Заключение
В этой статье я поделился некоторыми практическими наблюдениями и методами, которые помогают мне добиваться высоких результатов при плазменной резке металла. Надеюсь, мой опыт будет полезен другим специалистам, работающим в этой области. Обмен опытом и постоянное совершенствование технологий – залог развития металлообрабатывающей отрасли.