Прокачиваем плазменную резку: экспертные советы по улучшению качества кромки
Плазменная резка металла – технология, безусловно, популярная и востребованная. Но, как и в любом деле, дьявол кроется в деталях. Казалось бы, все просто: выставил ток, подал газ – и вперед. Но часто результат разочаровывает: неровная кромка, грат, деформация. Знакомо?
В этой статье я не буду разжевывать базовые принципы – вы, как профессионалы, и так с ними знакомы. Я поделюсь своим многолетним опытом и расскажу о нюансах, которые помогут вам выжать максимум из плазменной резки и добиться действительно безупречного качества кромки.
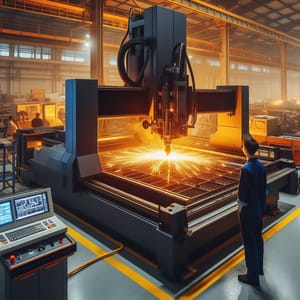
Неочевидные факторы, влияющие на качество кромки
Часто даже строгое соблюдение инструкций не гарантирует идеального результата. Почему? Потому что существуют факторы, которые производители оборудования скромно умалчивают.
Взаимодействие параметров дуги и газа:
Думаете, достаточно просто выставить рекомендованные значения тока и расхода газа? Увы, не все так просто. Эти параметры тесно взаимосвязаны, и изменение одного неизбежно влияет на другой.
Например, увеличение силы тока требует пропорционального увеличения расхода плазмообразующего газа. В противном случае возникает риск перегрева сопла и электрода, что приведет к их преждевременному износу и снижению качества реза.
Из своего опыта скажу, что на практике часто приходится экспериментально подбирать оптимальное соотношение тока и расхода газа, отклоняясь от стандартных рекомендаций.
"Скрытые" параметры плазмотрона:
В инструкциях к плазмотронам обычно указываются основные параметры, такие как сила тока, напряжение, расход газа. Но есть и другие, менее очевидные, но не менее важные настройки, которые могут существенно влиять на качество кромки.
Ток пилотной дуги:
Пилотная дуга — это своеобразный "запал", который инициирует основную режущую дугу. Ее ток определяет устойчивость зажигания и стабильность работы плазмотрона на начальном этапе. Слишком низкий ток может приводить к тому, что дуга будет "рваться" при прошивке металла, что негативно скажется на качестве кромки. Слишком высокий ток пилотной дуги грозит чрезмерным углублением в металл в начале реза и образованием "ямки".
Время перехода на режущую дугу:
Этот параметр определяет, как быстро плазмотрон переключается с пилотной дуги на основную режущую после прошивки металла. Оптимальное время перехода зависит от толщины металла и скорости резки. Если переключение произойдет слишком рано, режущая дуга может не успеть стабилизироваться, что приведет к неровностям на кромке. Слишком поздний переход грозит перегревом металла и образованием грата.
"Эффект бабочки" при плазменной резке:
Иногда даже при казалось бы идентичных настройках качество кромки может значительно отличаться при резке металла из разных партий. Виной тому — небольшие вариации в химическом составе металла, которые могут существенно влиять на процесс плазменной резки.
Например, даже небольшое увеличение содержания углерода в стали может привести к повышенному гратообразованию. А присутствие в составе металла таких элементов, как сера или фосфор, способно вызвать нестабильность плазменной дуги и ухудшение качества реза.
Зависимость качества реза от геометрии детали:
Резать ровные листы — это одно. Но что делать, если нужно вырезать деталь сложной формы с углами, изгибами и малыми отверстиями? Вот тут-то и начинаются настоящие сложности.
Углы:
При резке углов плазменная дуга стремится "срезать" их, что приводит к образованию дефектов на кромке. Чтобы минимизировать этот эффект, необходимо снижать скорость резки в углах и использовать специальные режимы плазмотрона с функцией компенсации углового отклонения.
Малые отверстия:
Резка отверстий малого диаметра (менее толщины металла) — задача не из легких. Здесь важно точно рассчитать энергию дуги и скорость резки, чтобы не допустить прожогов и деформаций.
Тонкие перемычки:
При резке деталей с тонкими перемычками существует риск их перегрева и деформации. В таких случаях эффективно применять пульсирующие режимы резки и охлаждение зоны реза сжатым воздухом.
High Definition Plasma и Water Injection Plasma: раскрываем потенциал
Стандартная плазменная резка хороша для многих задач, но что делать, когда требования к качеству кромки растут? Вот тут на помощь приходят продвинутые технологии — High Definition Plasma (HD Plasma) и Water Injection Plasma (WIP).
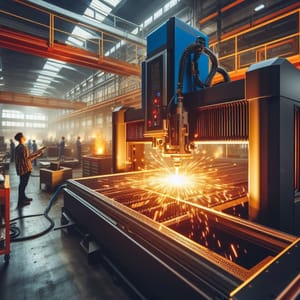
HD Plasma: тонкости, о которых не пишут в инструкциях
HD Plasma — это уже не просто "крутая штуковина", а необходимость для многих современных производств. Но даже самое передовое оборудование не даст желаемого результата, если не знать некоторых секретов.
Влияние чистоты газа на ресурс расходников и качество кромки:
Многие недооценивают важность чистоты плазмообразующего газа для HD Plasma. А между тем, даже незначительные примеси влаги, масла или других веществ могут привести к ускорению износа расходных материалов — сопла и электрода.
Из личного опыта: однажды столкнулся с ситуацией, когда после замены редуктора на газовом баллоне ресурс сопел резко снизился. Выяснилось, что новый редуктор был недостаточно герметичным, и в газ попадал воздух. Проблема ушла после установки качественного редуктора и продувки газовой магистрали.
Оптимизация параметров HD Plasma для резки высоколегированных сталей и алюминия:
Резка высоколегированных сталей и алюминия — отдельная история. Эти материалы требуют особого подхода и тщательной настройки параметров HD Plasma.
Например, для резки нержавеющей стали важно использовать смеси газов с повышенным содержанием азота, чтобы предотвратить окисление кромки. А при резке алюминия необходимо учитывать его высокую теплопроводность и подбирать режимы резки с умеренной энергией дуги.
"Подводные камни" HD Plasma:
Как и у любой технологии, у HD Plasma есть свои нюансы. Вот несколько распространенных ошибок, которые совершают даже опытные специалисты:
- Использование завышенной силы тока: да, хочется резать быстрее, но это часто приводит к перегреву металла и ухудшению качества кромки.
- Неправильный выбор газа: экономия на газах — плохая идея. Используйте только рекомендованные производителем типы и смеси газов.
- Пренебрежение охлаждением: эффективная система охлаждения — залог долговечности плазмотрона и стабильности реза.
Water Injection Plasma: выжимаем максимум из технологии
Water Injection Plasma (WIP) — это уже тяжелая артиллерия в мире плазменной резки. Если вам нужно резать толстые металлы (от 50 мм и выше) с максимально возможным качеством, без WIP не обойтись.
Как добиться максимально гладкой кромки при резке толстых металлов с помощью WIP:
Секрет успеха при резке толстых металлов методом WIP — в правильном сочетании нескольких факторов:
- Мощность дуги: для резки толстых металлов требуется высокая мощность дуги, но важно найти баланс между скоростью резки и качеством кромки.
- Расход воды: вода в WIP выполняет несколько функций — охлаждает дугу, сжимает плазменный столб, улучшает удаление расплавленного металла. Оптимальный расход воды зависит от толщины и типа металла, а также от мощности дуги.
- Геометрия сопла: для WIP используются специальные сопла с дополнительными каналами для подачи воды. Форма и размеры сопла подбираются индивидуально под конкретную задачу.
Нестандартные применения WIP:
WIP — универсальная технология, которая применяется не только для прямолинейной резки листов. Вот несколько примеров из моего опыта:
- Резка труб: WIP позволяет резать трубы большого диаметра с высокой точностью и чистотой кромки.
- Резка под углом: с помощью WIP можно резать металл под углом, что значительно расширяет возможности технологии.
Сравнение разных систем WIP:
На рынке представлено множество систем WIP от разных производителей. Как выбрать оптимальный вариант?
Обращайте внимание на следующие параметры:
- Максимальная толщина резаемого металла: у разных систем она может варьироваться от десятков миллиметров до 150 мм и более.
- Точность и качество реза: здесь важную роль играют конструктивные особенности плазмотрона и системы управления.
- Надежность и ресурс расходников: от этого напрямую зависят эксплуатационные расходы.
Нестандартные приемы для идеальной кромки: мой личный опыт
В мире металлообработки, как и в любом другом, стандартные решения не всегда приводят к оптимальному результату. Иногда приходится идти на хитрости, экспериментировать, искать нестандартные подходы. Именно таким опытом я и хочу с вами поделиться.
"Гибкая" плазменная резка:
Кто сказал, что нельзя комбинировать разные технологии и методы в рамках одного производственного процесса? На практике "гибкость" — залог эффективности.
Например, при изготовлении деталей сложной формы я часто комбинирую плазменную резку с лазерной. Сначала вырезаю основной контур детали на плазме (это быстро и относительно недорого), а затем делаю высокоточные резы и отверстия на лазере.
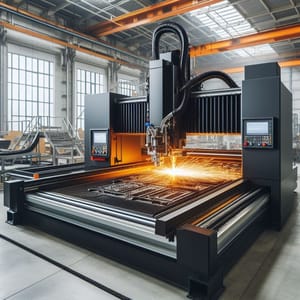
Создание собственных режимов резки:
Не бойтесь отходить от стандартных настроек плазмотрона! Конечно, начинать всегда лучше с рекомендаций производителя. Но для нестандартных материалов и задач часто приходится создавать собственные режимы резки.
Как я это делаю:
- Тщательно анализирую задачу: какой материал нужно резать, какая толщина, какие требования к качеству кромки.
- Подбираю исходные параметры: ориентируюсь на рекомендации производителя и свой предыдущий опыт.
- Провожу серию тестовых резов: меняю параметры небольшими шагами, внимательно наблюдая за результатом и фиксируя изменения.
- Анализирую полученные данные: выбираю оптимальные параметры, при которых достигается наилучшее соотношение скорости и качества реза.
Работа с "проблемными" металлами:
Титан, медь, латунь — эти материалы могут доставить немало хлопот при плазменной резке. Вот несколько советов, которые помогут справиться с этими "капризулями":
- Титан: чувствителен к перегреву, поэтому важно использовать высокую скорость резки и активное охлаждение.
- Медь и латунь: обладают высокой теплопроводностью, что требует применения повышенной мощности дуги.
Продлеваем жизнь расходникам:
Расходные материалы — сопла, электроды, защитные экраны — это то, на чем экономить не стоит. Но и выбрасывать их раньше времени тоже ни к чему.
Мои приемы продления жизни расходникам:
- Правильный подбор: не всегда нужно гнаться за самыми дорогими. Важно выбирать расходники, оптимальные для конкретных материалов и режимов резки.
- Соблюдение режимов: перегрев — главный враг расходников. Снижайте силу тока и скорость реза при работе с тонкими материалами.
- Чистота — залог здоровья: регулярно продувайте плазмотрон сжатым воздухом, чтобы удалить загрязнения, которые ускоряют износ.
- Своевременная замена: не ждите, пока сопло или электрод полностью выйдут из строя. Заменяйте их превентивно, чтобы не допустить снижения качества реза.
Разбор полетов: анализируем и учимся на ошибках
Как говорится, на чужих ошибках учиться легче. Поэтому я решил поделиться с вами двумя случаями из своей практики, которые наглядно демонстрируют, как важно учитывать все нюансы при плазменной резке.
Случай №1: "Загадочный" грат на нержавейке
Однажды мы получили заказ на изготовление партии деталей из нержавеющей стали с повышенными требованиями к качеству кромки. Вроде бы все делали "по науке": использовали HD Plasma, подобрали оптимальные режимы резки, применили аргон в качестве плазмообразующего газа. Но результат нас не устроил — на кромке постоянно образовывался небольшой, но все же заметный грат.
В чем же была причина?
После тщательного анализа мы выяснили, что виноват... газовый редуктор! Дело в том, что старый редуктор, который мы использовали, был не приспособлен для работы с аргоном. Из-за этого в газ попадал кислород из воздуха, что и приводило к окислению кромки и образованию грата.
Решение проблемы: замена газового редуктора на специализированный, предназначенный для работы с инертными газами.
Вывод: даже самая незначительная, на первый взгляд, деталь может существенно влиять на результат.
Случай №2: Тонкий металл — тонкая настройка
Как-то раз нам потребовалось изготовить партию мелких деталей из тонколистовой стали толщиной всего 1,5 мм. Казалось бы, что может быть проще? Но и здесь нас поджидали сложности.
При резке на стандартных режимах на кромке образовывались сильные деформации и прожоги. Пришлось попотеть, чтобы найти оптимальное решение.
Что мы сделали:
- Снизили силу тока: для тонкого металла важно использовать минимально возможную силу тока, чтобы не перегревать его.
- Увеличили скорость резки: это позволяет снизить тепловое воздействие на металл и предотвратить его деформацию.
- Поэкспериментировали с расстоянием от сопла до поверхности металла: для тонкого металла оно должно быть немного меньше, чем для толстого.
- Применили пульсирующий режим резки: это позволило еще больше снизить тепловую нагрузку на металл и получить более чистую кромку.
Результат: нам удалось добиться отличного качества кромки без деформаций и прожогов.
Вывод: при работе с тонким металлом важно быть особенно внимательными к настройкам плазмотрона и не бояться экспериментировать.
Плазменная резка будущего: тенденции и перспективы
Плазменная резка не стоит на месте. Технологии постоянно развиваются, открывая новые горизонты в мире металлообработки.
Что ждет нас в будущем?
- Еще выше точность и скорость: новые плазмотроны с улучшенной системой управления позволят добиться еще большей точности и скорости реза, что особенно актуально для изготовления деталей сложной формы.
- Новые возможности для работы с материалами: разрабатываются новые составы плазмообразующих газов и режимы резки, которые позволят эффективно обрабатывать даже самые сложные и тугоплавкие материалы.
- "Умные" системы: системы автоматизации и контроля с элементами искусственного интеллекта возьмут на себя рутинные операции по настройке и контролю процесса резки, что позволит минимизировать влияние человеческого фактора и повысить качество продукции.
- Экологичность: все большее внимание уделяется разработке экологически чистых технологий плазменной резки с использованием безвредных для окружающей среды газов и минимизацией отходов производства.
Главное — не бояться экспериментировать, постоянно совершенствовать свои навыки и внедрять передовые технологии. Тогда плазменная резка всегда будет для вас источником новых возможностей и высоких результатов.