Влияние частоты импульсов на процесс лазерной резки толстых листов
Лазерная резка – один из самых востребованных методов раскроя металла, особенно когда речь идет о толстых листах. При этом даже опытные инженеры порой сталкиваются с трудностями при обработке высокопрочных сталей, где критичным становится влияние частоты импульсов лазера на формирование зоны термического влияния (ЗТВ). Некорректно подобранный режим работы оборудования может привести к нежелательным изменениям в структуре металла, снижению прочности в зоне реза и появлению дефектов.
В данной статье мы рассмотрим, как вариация частоты импульсов влияет на геометрические параметры реза и свойства ЗТВ, а также разберем практические примеры решения нестандартных задач, с которыми сталкиваются специалисты при внедрении лазерной резки металла с помощью компании НСК Системс.
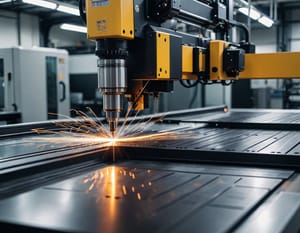
Частота импульсов и ее влияние на качество реза
Частота импульсов лазера - один из ключевых параметров, определяющих эффективность и качество лазерной резки. Она представляет собой количество импульсов, генерируемых лазером в секунду (Гц), и непосредственно влияет на количество тепловой энергии, передаваемой в материал за единицу времени.
Влияние на глубину прореза
Увеличение частоты импульсов, как правило, приводит к уменьшению глубины прореза за один проход. Это связано с тем, что при более высокой частоте импульсов на обработку одной и той же площади поверхности тратится меньше времени, следовательно, и меньше энергии успевает проникнуть в глубь материала.
Таблица 1. Зависимость глубины прореза от частоты импульсов для стали 09Г2С (толщина листа 10 мм, мощность лазера 4 кВт)
Частота импульсов, Гц | Глубина прореза, мм |
---|---|
200 | 10 |
500 | 8 |
1000 | 6 |
Данные в таблице являются приблизительными и могут меняться в зависимости от конкретной марки лазера и условий резки.
Влияние на ширину реза и шероховатость поверхности
С увеличением частоты импульсов ширина реза, как правило, уменьшается, а шероховатость обрабатываемой поверхности может как снижаться, так и возрастать в зависимости от сочетания параметров резки. Это связано с тем, что при более высокой частоте импульсов зона расплава металла становится более узкой и контролируемой. Однако, при неправильно подобранных параметрах резки может наблюдаться эффект "перегрева" и увеличения шероховатости.
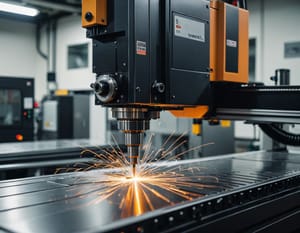
Формирование зоны термического влияния
Зона термического влияния (ЗТВ) – это область вокруг реза, которая подвергается нагреванию, но не расплавляется. Размер и свойства ЗТВ оказывают существенное влияние на качество изделия. Увеличение частоты импульсов обычно приводит к уменьшению ширины ЗТВ, так как тепловая энергия сосредотачивается на более узком участке.
Выбор оптимальной частоты импульсов: факторы и расчеты
Выбор оптимальной частоты импульсов – это многофакторная задача, требующая учета целого ряда параметров:
-
Толщина и тип материала: для резки толстых листов из высокопрочных сталей может потребоваться снижение частоты импульсов для обеспечения достаточного количества энергии для прореза, в то время как для тонколистовых материалов и низкоуглеродистых сталей оптимальной может оказаться более высокая частота.
-
Требования к качеству реза: если на первый план выходит чистота и гладкость кромки, то может потребоваться увеличение частоты импульсов. Если же приоритетом является скорость резки, то снижение частоты импульсов может дать выигрыш во времени обработки.
-
Технические характеристики лазерного оборудования:
- Тип лазера: разные типы лазеров (волоконные, CO2, твердотельные) имеют разные характеристики импульса, что непосредственно влияет на выбор оптимальной частоты.
- Волоконные лазеры, например, способны генерировать импульсы очень короткой длительности с высокой частотой следования, что делает их предпочтительными для резки тонких листов с высокой точностью.
- CO2 лазеры, напротив, чаще используются с более низкой частотой импульсов, что обусловлено их физическими особенностями.
- Мощность лазера: с увеличением мощности становится возможным использование более высоких частот импульсов без риска недореза.
- Система управления лазером: современные системы ЧПУ позволяют гибко регулировать частоту импульсов в широком диапазоне, что открывает широкие возможности для оптимизации процесса резки.
- Тип лазера: разные типы лазеров (волоконные, CO2, твердотельные) имеют разные характеристики импульса, что непосредственно влияет на выбор оптимальной частоты.
Примеры формул и расчетов
1. Определение зависимости глубины прореза (h) от частоты импульсов (f):
h = k / (f)^m
где:
- k - коэффициент, зависящий от мощности лазера, типа материала, давления газа и других параметров;
- m - показатель степени, обычно принимается равным 0.5-0.8.
Пример:
Пусть k = 2, m = 0.6, f1 = 200 Гц, f2 = 500 Гц. Тогда:
- h1 = 2 / (200)^0.6 ≈ 0.5 см
- h2 = 2 / (500)^0.6 ≈ 0.32 см
Вывод: увеличение частоты импульсов с 200 Гц до 500 Гц приведет к уменьшению глубины прореза примерно на 36%.
2. Расчет ширины зоны термического влияния (b):
b = a * (P / f)^n
где:
- a - коэффициент, зависящий от теплофизических свойств материала;
- P - мощность лазера;
- n - показатель степени, зависящий от режимов резки и типа материала.
Пример:
Допустим, a = 0.1, P = 3 кВт, n = 0.3, f1 = 100 Гц, f2 = 400 Гц. Тогда:
- b1 = 0.1 * (3000 / 100)^0.3 ≈ 0.22 мм
- b2 = 0.1 * (3000 / 400)^0.3 ≈ 0.16 мм
Вывод: увеличение частоты импульсов с 100 Гц до 400 Гц позволит сузить ЗТВ примерно на 27%.
Важно помнить, что приведенные формулы являются упрощенными и служат лишь для приблизительной оценки влияния частоты импульсов. На практике необходимо учитывать множество других факторов и проводить экспериментальную настройку параметров резки.
Нетривиальные кейсы и решения
В этом разделе я хочу поделиться несколькими случаями из моей практики, где правильный выбор частоты импульсов сыграл решающую роль в достижении требуемого результата.
Кейс 1: Резка листа нержавеющей стали толщиной 12 мм с минимальной ЗТВ
Задача: требовалось вырезать сложную деталь из листа нержавеющей стали марки AISI 316L толщиной 12 мм. При этом критичным требованием было минимизировать ширину ЗТВ, чтобы избежать последующей механической обработки.
Решение: стандартные режимы резки, предлагаемые производителем оборудования, давали ЗТВ шириной около 0.8 мм, что было неприемлемо. После анализа ситуации и проведения серии экспериментов было принято решение significantly снизить частоту импульсов до 150 Гц и одновременно увеличить скорость резания на 20%.
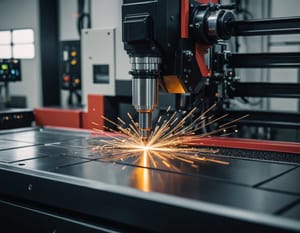
Результат: в результате удалось получить ЗТВ шириной не более 0.4 мм без потери качества реза, что позволило отказаться от дополнительной обработки детали.
Кейс 2: Повышение производительности резки конструкционной стали при сохранении геометрии реза
Задача: стояла задача оптимизировать процесс резки листов конструкционной стали марки Ст3сп толщиной 8 мм для увеличения производительности линии. При этом важно было сохранить заданную ширину реза (не более 1.2 мм) и избежать образования грата.
Решение: анализ показал, что использование стандартных режимов резки с высокой частотой импульсов (800 Гц) позволяет получить качественный рез, но скорость обработки ограничена. Было принято решение снизить частоту импульсов до 300 Гц и одновременно увеличить скорость подачи листа на 35%. Для компенсации снижения энергии импульса мощность лазера была увеличена на 15%.
Результат: снижение частоты импульсов позволило увеличить скорость резки без ущерба для ее качества. Ширина реза осталась в пределах допустимых значений (1.1 мм), грат не образовывался. Производительность линии удалось увеличить на 25%.
Кейс 3: Борьба с эффектом перегрева при резке титанового сплава
Задача: требовалось вырезать серию деталей сложной формы из титанового сплава ВТ6 толщиной 4 мм. При использовании стандартных режимов резки наблюдалось образование окалины и ухудшение качества поверхности в зоне реза.
Решение: анализ показал, что причина проблемы - в перегреве материала из-за слишком высокой частоты импульсов (1000 Гц). Для снижения теплового воздействия частоту импульсов снизили до 400 Гц, а для компенсации снижения энергии импульса увеличили мощность лазера на 10% и снизили скорость резки на 15%.
Результат: снижение частоты импульсов позволило избавиться от эффекта перегрева и получить чистую и гладкую поверхность реза без окалины.
Заключение
Влияние частоты импульсов на процесс лазерной резки толстых листов - сложный и многогранный вопрос, требующий от инженера глубокого понимания физики процесса и особенностей используемого оборудования. Не существует универсальных рецептов, и выбор оптимальных параметров всегда индивидуален.
Тем не менее, накопленный опыт и понимание базовых принципов, описанных в данной статье, позволяют успешно решать даже нестандартные задачи, повышая качество продукции и эффективность производства. Важно помнить, что эксперимент и анализ полученных результатов - неотъемлемая часть работы с современными лазерными комплексами.
Будущее лазерной резки связано с дальнейшим развитием технологий, появлением новых материалов и источников лазерного излучения. Однако, уверен, что умение тонко настраивать и контролировать такие параметры, как частота импульсов, всегда будет отличать высококлассного специалиста в области металлообработки.